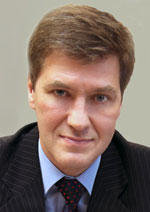
Nikiforov
Vladimir O.
D.Sc., Prof.
doi: 10.17586/2226-1494-2016-16-2-244-250
DESIGNING FEATURES OF POWER OPTICAL UNITS FOR TECHNOLOGICAL EQUIPMENT
Read the full article

For citation: Afanasyev M.Ya., Fedosov Yu.V., Nemkova A.A. Designing features of power optical units for technological equipment. Scientific and Technical Journal of Information Technologies, Mechanics and Optics, 2016, vol. 16, no. 2, pp. 244–250, doi:10.17586/2226-1494-2016-16-2-244-250
Abstract
This paper considers the question of an optical unit designing for transmitting power laser radiation through an optical fiber. The aim of this work is designing a simple construction unit with minimized reflection losses. The source of radiation in the optical unit described below is an ultraviolet laser with diode pumping. We present the general functioning scheme and designing features for the three main parts: laser beam deflecting system, laser beam dump and optical unit control system. The described laser beam deflection system is composed of a moving flat mirror and a spherical scattering mirror. Comparative analysis of the production technology for such mirrors was carried out, and, as a result, the decision was made to produce both mirrors of 99.99 % pure molybdenum without coating. A moving mirror deflects laser emission from a source through a fiber or deflects it on a spherical mirror and into the laser beam dump, moreover, switching from one position to another occurs almost immediately. It is shown that a scattering mirror is necessary, otherwise, the absorbing surface of the beam dump is being worn out irregularly. The laser beam dump is an open conical cavity, in which the conical element with its spire turned to the emission source is placed. Special microgeometry of the internal surface of the beam dump is suggested for the better absorption effect. An optical unit control system consists of a laser beam deflection system, laser temperature sensor, deflection system solenoid temperature sensor, and deflection mirror position sensor. The signal processing algorithm for signals coming from the sensors to the controller is described. The optical unit will be used in special technological equipment.
Acknowledgements. We thank our colleagues, Nikita B. Margaryants and Galina E. Romanova, for assistance in carrying out experiments and computer modeling.
References
1. Tsoukantas G., Salonitis K., Stournaras A., Stavropoulos P., Chryssolouris G. On optical design limitations of generalized two-mirror remote beam delivery laser systems: the case of remote welding. International Journal of Advanced Manufacturing Technology, 2007, vol. 32, no. 9–10, pp. 932–941. doi: 10.1007/s00170-005-0400-7
2. Ussing T., Petersen L.V., Nielsen C.B., Helbo B., Hojslet, L. Micro laser welding of polymer microstructures using low power laser diodes. International Journal of Advanced Manufacturing Technology, 2007, vol. 33, no. 1–2, pp. 198–205. doi: 10.1007/s00170-007-0969-0
3. Kuhn A., Blewett I.J., Hand D.P., French P., Richmond M., Jones J.D.C. Optical fiber beam delivery of high-energy laser pulses: beam quality preservation and fiber end-preparation. Optics and Lasers in Engineering, 2000, vol. 34, no. 4–6, pp. 273–288. doi: 10.1016/S0143-8166(00)00082-8
4. Vychislitel'naya Optika: Spravochnik [Computational Optics: A Handbook]. / Eds. M.M. Rusinov, A.P. Grammatin, P.D. Ivanov et. al. Moscow, Mashinostroenie Publ., 1984, 423 p.
5. Zapryagaeva L.A., Sveshnikova I.S. Raschet i Proektirovanie Opticheskikh System [Calculation and Design of Optical Systems]. Moscow, Logos Publ., 2000, 584 p.
6. Roikh I.L. Nanesenie Zashchitnykh Pokrytii v Vakuume. Pokrytiya [Creating of Protective Coating in Vacuum. Coatings]. Available at: http://de.ifmo.ru/bk_netra/page.php?tutindex=46&index=28&layer=1 (accessed 10.02.2016).
7. Galyautdinov R.T., Kashapov N.F., Luchkin G.S. Formation of protective coatings for aluminium mirrors by magnetron sputtering. Welding International, 2003, vol. 17, no. 8, pp. 655–658. doi: 10.1533/wint.2003.3184
8. Temperaturnyi Koeffitsient Lineinogo Rasshireniya [Temperature Coefficient of Linear Expansion]. Available at: http://temperatures.ru/pages/temperaturnyi_koefficient_lineinogo_rasshireniya (accessed 15.02.2016).
9. Solk S.V. Development and Research of Technological Methods of Manufacturing, Control and Adjusting of the Optical Elements and Devices of Infrared Equipment. Dis. Dr. Eng. Sciences. St. Petersburg, ITMO University, 2015, 287 p. (In Russian)
10. Naumov M.B. Lazernye Silovye Zerkala [Laser Power Mirrors]. Moscow, MIREA Publ., 2008, 171 p.
11. Lakhtin Yu.M., Leont'eva V.P. Materialovedenie: Uchebnik [Material Science: Textbook]. 3rd ed. Moscow, Mashinostroenie Publ., 1990, 528 p.
12. Kharakteristiki Materiala BrKh. Marochnik Stali i Splavov [Characteristics of BrH material. Grade Guide of Steel and Allows]. Available at: http://www.splav-kharkov.com/mat_start.php?name_id=1189 (accessed 16.02.2016).
13. Yoshida K., Takeuchi K., Kato Y., Fujiwara E., Yamashita K., Kurosawa K., Sasaki W., Okamoto H. Superpolished single crystal molybdenum mirror for x-ray ultraviolet to x-ray radiation. Applied Physics, 1988, vol. 52, no. 14, pp. 1111–1113. doi: 10.1063/1.99177
14. Leontyev A., Semerok A., Farcage D., Thro P.-Y., Grisolia C., Widdowson A., Coad P., Rubel M. Theoretical and experimental studies on molybdenum and stainless steel mirrors cleaning by high repetition rate laser beam. Fusion Engineering and Design, 2011, vol. 86, no. 9–11, pp. 1728–1731. doi: 10.1016/j.fusengdes.2010.12.068
15. Sherwood B.J. Molybdenum laser mirrors. Metal Finishing, 2008, vol. 106, no. 4, pp. 87–88.
16. Mizusawa M., Sakurai K. Specular and non-specular X-ray reflection from a single-crystal molybdenum mirror surface. Nuclear Instruments and Methods in Physics Research Section B: Beam Interactions with Materials and Atoms, 2003, vol. 199, pp. 139–142. doi: 10.1016/S0168-583X(02)01621-X
17. Alyuminii D16 Duralyumin D16, Dyural' D16 [Aluminum D16 Duralumin D16]. Available at: http://metallicheckiy-portal.ru/marki_metallov/alu/D16 (accessed 14.02.2016).
18. Gonzalez F., Barrera E.C., Rosas R.C. Photothermal selective coatings of black molybdenum. Revista Mexicana de Ingeniera Qumica, 2010, vol. 9, no. 1, pp. 79–83.