Menu
Publications
2025
2024
2023
2022
2021
2020
2019
2018
2017
2016
2015
2014
2013
2012
2011
2010
2009
2008
2007
2006
2005
2004
2003
2002
2001
Editor-in-Chief
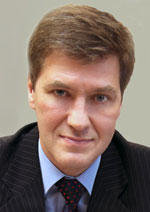
Nikiforov
Vladimir O.
D.Sc., Prof.
Partners
doi: 10.17586/2226-1494-2023-23-4-820-827
Modeling and simulation of heat exchanger with strong dependence of oil viscosity on temperature
Read the full article

Article in Russian
For citation:
Abstract
For citation:
Kurmanova D.E., Jaichibekov N.Zh. Modeling and simulation of heat exchanger with strong dependence of oil viscosity on temperature. Scientific and Technical Journal of Information Technologies, Mechanics and Optics, 2023, vol. 23, no. 4, pp. 820–827 (in Russian). doi: 10.17586/2226-1494-2023-23-4-820-827
Abstract
Heating of oil and oil products is widely used to reduce energy losses during transportation. The flow in the annular space of the heat exchanger is complex and depends on many factors. The use of thin tubes in helicoid-type heat exchangers makes it necessary to take into account the transition of the flow regime from laminar to turbulent. The semi-empirical turbulence models traditionally used in numerical calculations do not take into account the laminar-turbulent transition. An approach is developed to determine the effective length of the heat exchanger and the temperature of the cold coolant at its outlet in the case of a strong dependence of oil viscosity on temperature, taking into account the possibility of a laminar-turbulent transition. Oil is considered as a heated coolant, and water is considered as a heating component. The novelty of the developed approach lies in the application of the turbulence model, which takes into account the laminar-turbulent transition, to the calculation of helicoid-type heat exchangers. For numerical simulation, the Reynolds-averaged Navier–Stokes equations are used which are closed using γ–Reθt turbulence model that takes into account the laminar-turbulent transition. The results of numerical calculations are compared with the data obtained on the basis of the log-mean temperature difference method at constant and variable viscosity. In the case of variable oil viscosity, a transition from the laminar flow regime to the turbulent one is manifested which has a significant effect on the effective length of the heat exchanger. The results of numerical calculations can be useful in designing helicoid-type heat exchangers.
Keywords: energy, heat transfer, viscosity, hydrodynamics, oil products, simulation, laminar and turbulent transition
References
References
- Nakaso K., Mitani H., Fukai J. Convection heat transfer in a shell-and-tube heat exchanger using sheet fins for effective utilization of energy. International Journal of Heat and Mass Transfer, 2015, vol. 82, pp. 581–587. https://doi.org/10.1016/j.ijheatmasstransfer.2014.11.033
- Wang Y., Gu X., Jin Z., Wang K. Characteristics of heat transfer for tube banks in crossflow and its relation with that in shell-and-tube heat exchangers. International Journal of Heat and Mass Transfer, 2016, vol. 93, pp. 584–594. https://doi.org/10.1016/j.ijheatmasstransfer.2015.10.018
- Araavind S., Athreya A.S. CFD analysis of shell and tube heat exchanger for pre-heating of biodiesel. International Journal of Advance Research in Science and Engineering, 2017, vol. 6, no. 7, pp. 687–693.
- Abda A.A., Kareema M.Q., Najib S.Z. Performance analysis of shell and tube heat exchanger: parametric study. Case Studies in Thermal Engineering, 2018, vol. 12, pp. 563–568. https://doi.org/10.1016/j.csite.2018.07.009
- Lychakov V.D., Scheglov A.A., Sivovolov A.S., Matyash A.S., Balunov B.F., Egorov M.Y. An analysis of heat transfer in assemblies of finned heat-exchange elements. Thermal Engineering, 2022, vol. 69, no. 3, pp. 202–209. https://doi.org/10.1134/S0040601522030089
- Darbandi M., Abdollahpour M.-S., Hasanpour-Matkolaei M. A new developed semi-full-scale approach to facilitate the CFD simulation of shell and tube heat exchangers. Chemical Engineering Science, 2021, vol. 245, pp. 116836. https://doi.org/10.1016/j.ces.2021.116836
- Bizhan K.G., Mohammad R.D., Hossein P. Prediction of kinematic viscosity of petroleum fractions using artificial neural networks. Iranian Journal of Oil and Gas Science and Technology, 2014, vol. 3, no. 2, pp. 51–65.
- Boda M.A., Bhasagi P.N., Sawade A.S., Andodgi R.A. Analysis of kinematic viscosity for liquids by varying temperature. International Journal of Innovative Research in Science, Engineering and Technology, 2015, vol. 4, no. 4, pp. 1951–1954. https://doi.org/10.15680/IJIRSET.2015.0404020
- Lee B.I., Kesler M.G. A generalized thermodynamic correlation based on three-parameter corresponding states. AIChE Journal, 1975, vol. 21, no. 3, pp. 510–527. https://doi.org/10.1002/aic.690210313
- Aralov O.V., Buyanov I.V., Savanin A.S., Iordansky E.I. Research of methods for oil kinematic viscosity calculation in the oil-trunk pipeline. Science & Technologies: Oil and Oil Products Pipeline Transportation, 2017, vol. 7, no. 5, pp. 97–105. (in Russian)
- Yogesh S.S., Selvaraj A.S., Ravi D.K., Rajagopal T.K.R. Heat transfer and pressure drop characteristics of inclined elliptical fin tube heat exchanger of varying ellipticity ratio using CFD code. International Journal of Heat and Mass Transfer, 2018, vol. 119, pp. 26–39. https://doi.org/10.1016/j.ijheatmasstransfer.2017.11.094
- Chen K., Mohammed H.I., Mahdi J.M., Rahbari A., Cairns A., Talebizadehsardari P. Effects of non-uniform fin arrangement and size on the thermal response of a vertical latent heat triple-tube heat exchanger. Journal of Energy Storage, 2022, vol. 45, pp. 103723. https://doi.org/10.1016/j.est.2021.103723
- Osley W.G., Droegemueller P., Ellerby P. CFD investigation of heat transfer and flow patterns in tube side laminar flow and the potential for enhancement. Chemical Engineering Transactions, 2013, vol. 35, pp. 997–1002. https://doi.org/10.3303/CET1335166
- Karar O., Emani S., Gounder S.M., Myo Thant M.M., Mukhtar H., Sharifpur M., Sadeghzadeh M. Experimental and numerical investigation on convective heat transfer in actively heated bundle-pipe. Engineering Applications of Computational Fluid Mechanics, 2021, vol. 15, no. 1, pp. 848–864. https://doi.org/10.1080/19942060.2021.1920466
- Rana S., Zunaid M., Kumar R. CFD approach for the enhancement of thermal energy storage in phase change material charged heat exchanger. Case Studies in Thermal Engineering, 2022, vol. 33, pp. 101921. https://doi.org/10.1016/j.csite.2022.101921
- Allouche Y., Varga S., Bouden C., Oliveira A.C. Validation of a CFD model for the simulation of heat transfer in a tubes-in-tank PCM storage unit. Renewable Energy, 2016, vol. 89, pp. 371–379. https://doi.org/10.1016/j.renene.2015.12.038
- Balaji D., Prakash L.S.S. CFD analysis of a pressure drop in a staggered tube bundle for a turbulent cross flow. International Advanced Research Journal in Science, Engineering and Technology, 2016, vol. 3, no. 2, pp. 35–40. https://doi.org/10.17148/IARJSET.2016.3209
- Czarnota T., Wagner C. Turbulent convection and thermal radiation in a cuboidal Rayleigh–Bénard cell with conductive plates. International Journal of Heat and Fluid Flow, 2016, vol. 57, pp. 150–172. https://doi.org/10.1016/j.ijheatfluidflow.2015.10.006
- Mohanan A.K., Prasad B.V., Vengadesan S. Flow and heat transfer characteristics of a cross-flow heat exchanger with elliptical tubes. Heat Transfer Engineering, 2021, vol. 42, no. 21, pp. 1846–1860. https://doi.org/10.1080/01457632.2020.1826742
- Tugunov P.I., Novoselov V.F., Korshak A.A., Shammazov A.M. Standard Calculations for the Design and Operation Of Petrolium Storage Depots and Oil Pipelines. Moscow, Dizajn Poligraf Servis Publ., 2002, 234 p. (in Russian)
- Kirillov P.L., Iurev Iu.S., Bobkov V.P. Handbook of Thermal-Hydraulic Calculations (Nuclear-Power Reactors, Heat Exchangers, Steam Generating Units). Moscow, Jenergoatomizdat, 1990, 360 p. (in Russian)
- Petukhov B.S., Genin L.G., Kovalev S.A. Heat transfer in nuclear power plants. Moscow, Atomizdat Publ., 1974, 408 p. (in Russian)
- Kutateladze S.S. Heat Transfer and Hydrodynamical Resistance. Moscow, Jenergoatomizdat Publ., 1990, 367 p. (in Russian)
- Menter F.R. Two-equation eddy-viscosity turbulence models for engineering applications. AIAA Journal, 1994, vol. 32, no. 8, pp. 1598–1605. https://doi.org/10.2514/3.12149
- Menter F., Esch T., Kubacki S. Transition modelling based on local variables. Engineering Turbulence Modelling and Experiments, Elsevier, 2002, pp. 555–564. https://doi.org/10.1016/b978-008044114-6/50053-3
- Langtry R.B., Menter F.R. Correlation-based transition modeling for unstructured parallelized computational fluid dynamics codes. AIAA Journal, 2009, vol. 47, no. 12, pp. 2894–2906. https://doi.org/10.2514/1.42362
- Coder J.G., Maughmer M.D. Computational fluid dynamics compatible transition modeling using an amplification factor transport equation. AIAA Journal, 2014, vol. 52, no. 11, pp. 2506–2512. https://doi.org/10.2514/1.j052905
- Menter F.R., Smirnov P.E., Liu T., Avancha R. A one-equation local correlation-based transition model. Flow, Turbulence and Combustion, 2015, vol. 95, no. 4, pp. 583–619. https://doi.org/10.1007/s10494-015-9622-4
- Gorji S., Seddighi M., Ariyaratne C., Vardy A.E., O’Donoghue T., Pokrajac D., He S. A comparative study of turbulence models in a transient channel flow. Computers and Fluids, 2014, vol. 83, pp. 111–123. https://doi.org/10.1016/j.compfluid.2013.10.037
- Volkov K. Numerical analysis of Navier–Stokes equations on unstructured meshes. Handbook on Navier–Stokes Equations: Theory and Analysis. Nova Science, 2016, pp. 365–442.
- Volkov K. Multigrid and preconditioning techniques in CFD applications. CFD Techniques and Thermo-Mechanics Applications, Springer, 2018, pp. 83–149. https://doi.org/10.1007/978-3-319-70945-1_6