Menu
Publications
2024
2023
2022
2021
2020
2019
2018
2017
2016
2015
2014
2013
2012
2011
2010
2009
2008
2007
2006
2005
2004
2003
2002
2001
Editor-in-Chief
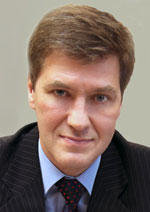
Nikiforov
Vladimir O.
D.Sc., Prof.
Partners
doi: 10.17586/2226-1494-2024-24-2-171-181
Selection of parameters of optoelectronic systems for monitoring the wear for steam turbine rotor blading based on the value of the total error
Read the full article

Article in Russian
For citation:
Abstract
For citation:
Rodikova L.S., Korotaev V.V., Timofeev A.N., Ryzhova V.A., Maraev A.A., Mikheev S.V. Selection of parameters of optoelectronic systems for monitoring the wear for steam turbine rotor blading based on the value of the total error. Scientific and Technical Journal of Information Technologies, Mechanics and Optics, 2024, vol. 24, no. 2, pp. 171–181 (in Russian). doi: 10.17586/2226-1494-2024-24-2-171-181
Abstract
Optoelectronic wear monitoring system of rotor blades of steam turbine low-pressure cylinders provide an assessment of the chord value of the working blade in static conditions on a closed cylinder. However, these systems do not allow the operator to assess the wear with the necessary error during shaft rotation. The control process is complicated by the fact that the output edge of the blade is overlapped by the input edge of the next blade; therefore it is necessary to set a scanning direction for each section that will ensure the formation of blade video frames, including both the input and output edges. The shaft rotation mode requires the use of pulsed illumination of the edges of the working blades to reduce the amount of image smudge; therefore it is necessary to select the focal length of the camera lens, the diameter of the entrance pupil of the lens and the power of pulsed radiation sources. The development of a methodology for selecting system parameters will help to reduce the complexity of designing systems for various turbine models and application technologies. Therefore, this is an important task. A methodology has been developed for selecting the parameters of the wear control systems of the working blades, which is based on the criterion of equality of the main components of the total error of the chord value. The analytical studies used the relationship of the parameters of the matrix receiver of optical radiation, illumination sources and the optical circuit with the required characteristics of the system. Computer modeling of the information conversion process in the system under study took into account the relationship between the parameters of the moving blades and the parameters of the optical circuit. The experimental estimation of the system error in statics and dynamics is based on multiple measurements after calibration of the system according to known parameters of the blades. When using the developed methodology, it is possible to achieve the required field of view and a given error in controlling the chord value, due to the choice of: matrix optical radiation receiver, focal length of the camera lens, diameter of the lens entrance pupil, and power of radiation sources. Using the example of the fifth stage of the vane device of the K-1200 high unit power turbine, which is most susceptible to wear, it is shown that for maximum values of the rotation angles of the video probe is 19° and the delay time of frame synchronization is up to 0.18 s, the focal length of the camera lens should be less than 2.4 mm with a pulse illumination time of 0.05 s. Computer modeling has shown that the marginal error of the system can reach 0.011 mm, which illustrates the possibility of reducing the total error. Using the developed methodology, the main elements were selected and a layout of the system was created. The requirements for exposure time and delay time of frame synchronization are formulated. The effectiveness of the parameter selection methodology was confirmed by experimental studies of the system layout, which showed that the estimate of the standard deviation of the random component of the chord control error in dynamics was 0.26 mm, which is three times less than that of the previously developed system and meets the requirements for evaluating the operability of the rotor blades of steam turbines during operation and repair. The proposed technique can be used by developers of other optoelectronic means of contactless control of linear dimensions of parts oriented non-perpendicular to the line of sight.
Keywords: steam turbine, rotor blades, erosive wear, rotor blade chord, wear control of the rotor blade, optoelectronic system, parameter selection
References
References
- Nazolin A.L. Prevention of accidents and disasters of rotating equipment for critically and strategically important technospheric facilities (based on the example of powerful turbine units of nuclear and thermal power plants): contribution report. Moscow, RAS, 2017, 40 p. (in Russian)
- Geng J., Xie J. Review of 3-D endoscopic surface imaging techniques. IEEE Sensors Journal, 2014, vol. 14, no. 4, pp. 945–960. https://doi.org/10.1109/jsen.2013.2294679
- Gorevoy A.V., Machikhin A.S., Khokhlov D.D., Batshev V.I., Kaloshin V.A., Perfilov A.M. Applying a ray tracing model of an optoelectronic system to improve the accuracy of endoscopic measurements. Russian Journal of Nondestructive Testing, 2017, vol. 53, no. 9, pp. 660–668. https://doi.org/10.1134/S1061830917090054
- Chichigin B.A., Groo I.A. Development of a small-scale high-speed system of measuring defectoscopy and its testing on different objects. Journal of Communications Technology and Electronics, 2022, vol. 67, no. 7, pp. 827–833. https://doi.org/10.1134/s1064226922070075
- Shchinnikov P.A., Nozdrenko G.V., Mikhailenko A.I., Dvortcevoi A.I., Safronov A.V. Automation and Management of Technological Processes at Thermal Power Plants. Novosibirsk, NSTU, 2014, 291 p. (in Russian)
- Khaimov V.A., Kokin E.Sh., Puzyrev E.I., Voronkov E.O., Ganzhin V.A. Implementation of a system for operational monitoring and diagnosis of working blades erosive wear in powerful steam turbines. Electrical Stations, 2006, no. 12, pp. 32‒36. (in Russian)
- Kasl J., Matějová M., Mrštík J. Failure analysis of rotating blades of lowpressure steam turbine rotors and possibility of prediction corrosion-fatigue ruptures. MATEC Web of Conferences, 2018, vol. 188, pp. 04020. https://doi.org/10.1051/matecconf/201818804020
- Shut G.A., Korotaev V.V., Puzyrev E.I., Ryzhova V.A., Timofeev A.N., Akhmerov A.H., Rodikova L.S. Videoendoscopy of working blades of steam turbines and control of their geometrical parameters. Journal of Optical Technology, 2020, vol. 87, no. 11, pp. 677‒683. https://doi.org/10.1364/jot.87.000677
- Low-Flow Modes of T-250/300-240 LPC Turbine. Ed. by V.A. Khaimov. St. Petersburg, BHV-Petersburg, 2007, 240 p. (in Russian)
- Leiner D. Digital Endoscope Design. SPIE, 2015. https://doi.org/10.1117/3.2235283
- Shut’ G.A., Puzyrev A.V., Vasileva A.V., Vasilev A.S., Nekrylov I.S., Akhmerov A.K., Timofeev A.N. Integrated endoscopy system for monitoring erosion wear of steam turbine blades. Journal of Instrument Engineering, 2020, vol. 63, no. 3, pp. 228–237. (in Russian). https://doi.org/10.17586/0021-3454-2020-63-3-228-236
- Todros K., Hero A.O. Measure-transformed quasi-maximum likelihood estimation. IEEE Transactions on Signal Processing, 2017, vol. 65, no. 3, pp. 748–763. https://doi.org/10.1109/tsp.2016.2621732
- Andreev A.L. Modeling and Calculation of Automated Video Information Systems for Objects Monitoring: Guidelines for laboratory work. St. Petersburg, NIU ITMO, 2013, 82 p. (in Russian)
- Uss M., Vozel B., Lukin V., Chehdi K. Potential accuracy of translation estimation between radar and optical images. Proceedings of SPIE, 2015, vol. 9643, pp. 96430W. https://doi.org/10.1117/12.2194071
- Tan Q., Kou Y., Miao J., Liu S., Chai B. A model of diameter measurement based on the machine vision. Symmetry, 2021, vol. 13, no. 2, pp. 187. https://doi.org/10.3390/sym13020187
- Pham N.T., Timofeev A.N., Korotaev V.V., Ryzhova V.A., Rodrigues J.J.P.C. An analysis of additional errors of the optical-electronic system for monitoring the railway track position. Scientific and Technical Journal of Information Technologies, Mechanics and Optics, 2021, vol. 21, no. 1, pp. 15–23. (in Russian). https://doi.org/10.17586/2226-1494-2021-21-1-15-23
- Starasotnikau M.A., Feodortsau R.V. Accuracy comparison of algorithms for determination of image center coordinates in optoelectronic devices. Science аnd Technique, 2018, vol. 17, no. 1, pp. 79–86. (in Russian). https://doi.org/10.21122/2227-1031-2018-17-1-79-86
- Pham N.T., Timofeev A.N., Nekrylov I.S. Study of the errors of stereoscopic optical-electronic system for railroad track position. Proceedings of SPIE, 2019, vol. 11056, pp. 110562F. https://doi.org/10.1117/12.2526081
- Potapov A.I., Kul’chitskii A.A., Smorodinskii Y.G. Analyzing the accuracy of a device for controlling the position of a rotating plane. Russian Journal of Nondestructive Testing, 2018, vol. 54, no. 11, pp. 757–764. https://doi.org/10.1134/S1061830918110086
- Korotaev V.V., Maraev A.A., Timofeev A.N. Beam Ride Using an Optical Equal-Signal Zone. St. Petersburg, ITMO University, 2015, 326 p. (in Russian)
- Nose A., Yamazaki T., Katayama H., Uehara S., Kobayashi M., Shida S., Odahara M., Takamiya K., Matsumoto S., Miyashita L., Watanabe Y., Izawa T., Muramatsu Y., Nitta Y., Ishikawa M. Design and performance of a 1 ms high-speed vision chip with 3D-stacked 140 GOPS column-parallel PEs. Sensors, 2018, vol. 18, no. 5, pp. 1313. https://doi.org/10.3390/s18051313
- Stefanov K.D., Clarke A.S., Ivory J., Holland A.D. Design and performance of a pinned photodiode CMOS image sensor using reverse substrate bias. Sensors, 2018, vol. 18, no. 1, pp. 118. https://doi.org/10.3390/s18010118
- Maraev A.A., Shut G.A., Timofeev A.N., Mikheev S.V., Akhmerov A.Kh., Rodikova L.S., Konyakhin I.A. Effect of illumination on errors in estimation of a rotor blade chord value during intelligent video endoscopy of a closed steam turbine cylinder. Studies in Systems, Decision and Control, 2022, vol. 419, pp. 169–185 https://doi.org/10.1007/978-3-030-97004-8_13
- Ting-Fa X., Peng Z. Image motion-blur-based object's speed measurement using an interlaced scan image. Measurement Science and Technology, 2010, vol. 21, no. 7, pp. 075502. https://doi.org/10.1088/0957-0233/21/7/075502
- Pham N.T., Pantyushina E.N., Timofeev A.N., Vasilev A.S., Dinh B.M. Influence of the speed of the optical-electronic system movement on the control error of the railway track position. Journal of Instrument Engineering, 2018, vol. 61, no. 9, pp. 814–822. (in Russian). https://doi.org/10.17586/0021-3454-2018-61-9-814-822