Menu
Publications
2024
2023
2022
2021
2020
2019
2018
2017
2016
2015
2014
2013
2012
2011
2010
2009
2008
2007
2006
2005
2004
2003
2002
2001
Editor-in-Chief
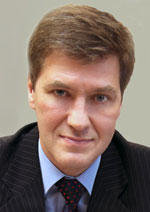
Nikiforov
Vladimir O.
D.Sc., Prof.
Partners
doi: 10.17586/2226-1494-2024-24-2-284-292
Models and a deformations simulation approach using ANSYS CAD for railway wagons weighing system
Read the full article

Article in Russian
For citation:
Abstract
For citation:
Denisenko M.A., Isaeva A.S., Sinyukin A.S., Kovalev A.V. Models and a deformations simulation approach using ANSYS CAD for railway wagons weighing system. Scientific and Technical Journal of Information Technologies, Mechanics and Optics, 2024, vol. 24, no. 2, pp. 284–292 (in Russian). doi: 10.17586/2226-1494-2024-24-2-284-292
Abstract
Possibility of fast, convenient and precise definition of wagons load mass allows enhancing transport safety and ensures assets accounting in railroad infrastructure. There are known three-dimensional solid models of railway track sector and approaches of simulation the deformation which emerge in rails by mechanical load effect transmitted through wagon wheels. In accordance with these approaches, emerging deformations are recomputed into wagons weight. The rail temperature influences on its mechanical properties and, consequently, on the deformation value. In this work, for the first time, a technique has been proposed that allows one to consider the deformation of the rail under the load influence, taking into account its temperature variance at different boundary conditions. According to the proposed approach, the wagon weight is defined by deformation values which are measured by strain gauges located on the rail web. The developed models include a rail wheel, ties and a rail fragment. The rail fragment corresponding to the railway track sector on which sensors are mounted geometrically replicates an existent rail type R50 and is situated on the ties fixed from bottom side. The wheel model complies with an existent solid-rolled wagon wheel type with tread diameter 920 mm, thereby correct contact patch retains in the model. According to the approach, finite-element mesh is generated on the developed solid models, connections between model fragments are established, and boundary and temperature conditions as well as acting forces are applied. Sequentially finite-element analysis is performed for all possible combination of wheel coordinate, load mass and temperature. For every case, deformation values are registered in four rail nodes corresponding to strain gauges placements. Comparison of finite-element analysis results for two developed solid models is carried out. The models differ by the way of the rail on the ties mounting and boundary condition setting on the end faces of the rail fragment, allowing to consider possibility of temperature stresses relaxation. In the model 1 the rail is connected with ties rigidly, in the model 2 the rail and the ties are connected by a contact allowing the rail motion along the tie with given friction coefficient. Besides that clamp bolts impact is imitated in the model 2. The approach is implemented within multiphysical simulation environment ANSYS for coupled three-dimensional problem using Static Structural and Steady-State Thermal modules. Simulation results showed that the deformation values determined by the temperature influence differ for the proposed models. Vertical deformations range of the rail fragment on which the strain gauges are fastened, at the mass 12,500 kg loaded on the wheel, is from –245 μm (bend down) to 15 μm (bend up) for the model 1 depending on the rail temperature (in the range from –20 °C to +50 °C) and from –225 μm to –100 μm for the model 2. This allows concluding that the model 2 reflects deformation process more correctly, and the temperature influence on the deformation is less relevant compared to mechanical load value. The proposed model in contrast to the known ones implies static weighing characterized by more accuracy, reliability and simplicity of use. In the future it is planned the executing of the more detail research of a model with two wheels and an axle for determining optimal simulation time and obtained results accuracy.
Keywords: railway monitoring system, loads identification, finite element method, solid state modeling, models updating
Acknowledgements. Работа выполнена в рамках проекта № FENW-2020-0022 «Разработка и исследование методов и средств мониторинга, диагностики и прогнозирования состояния инженерных объектов на основе искусственного интеллекта» по заданию Минобрнауки Российской Федерации.
References
Acknowledgements. Работа выполнена в рамках проекта № FENW-2020-0022 «Разработка и исследование методов и средств мониторинга, диагностики и прогнозирования состояния инженерных объектов на основе искусственного интеллекта» по заданию Минобрнауки Российской Федерации.
References
- Pau A., Vestroni F. Weigh-in-motion of train loads based on measurements of rail strains. Structural Control Health Monitoring, 2021, vol. 28, no. 11, pp. e2818. https://doi.org/10.1002/stc.2818
- Molodova M., Li Z., Núñez A., Dollevoet R. Automatic detection of squats in railway infrastructure. IEEE Transactions on Intelligent Transportation Systems, 2014, vol. 15, no. 5, pp. 1980–1990. https://doi.org/10.1109/TITS.2014.2307955
- Xu L., Zhai W. Train–track coupled dynamics analysis: system spatial variation on geometry, physics and mechanics. Railway Engineering Science, 2020, vol. 28, no. 1, pp. 36–53. https://doi.org/10.1007/s40534-020-00203-0
- Molodova M., Li Z., Dollevoet R. Axle box acceleration: measurement and simulation for detection of short track defects. Wear, 2011, vol. 271, no. 1-2, pp. 349–356. https://doi.org/10.1016/j.wear.2010.10.003
- Pintão B., Mosleh A., Vale C., Montenegro P., Costa P. Development and validation of a weigh-in-motion methodology for railway tracks. Sensors, 2022, vol. 22, no. 5, pp. 1976. https://doi.org/10.3390/s22051976
- Zakharenko M., Frøseth G.T., Rönnquist A. Train classification using a weigh-in-motion system and associated algorithms to determine fatigue loads. Sensors, 2022, vol. 22, no. 5, pp. 1772. https://doi.org/10.3390/s22051772
- Allota B., D’Adamio P., Marini L., Meli E., Pugi L., Rindi A. A new strategy for dynamic weighing in motion of railway vehicles. IEEE Transactions on Intelligent Transportation Systems, 2015, vol. 16, no. 6, pp. 3520–3533. https://doi.org/10.1109/TITS.2015.2477104
- Senyanskiy D.M. Problem of increasing the accuracy of railway carriages weighing in motion. Proc. of the XVII IMEKO World Congress Metrology in the 3rd Millennium, 2003, pp. 374–377.
- Mosleh A., Costa P.A., Calçada R. A new strategy to estimate static loads for the dynamic weighing in motion of railway vehicles. Proceedings of the Institution of Mechanical Engineers, Part F: Journal of Rail and Rapid Transit, 2020, vol. 234, no. 2, pp. 183–200. https://doi.org/10.1177/0954409719838115
- Mosleh A., Costa P.A., Calçada R. Development of a low-cost trackside system for weighing in motion and wheel defects detection. International Journal of Railway Research, 2020, vol. 7, no. 1, pp. 1–9.
- Costa B.J.A., Martins R., Santos M., Felgueiras C., Calçada R. Weighing-in-motion wireless system for sustainable railway transport. Energy Procedia, 2017, vol. 136, pp. 408–413. https://doi.org/10.1016/j.egypro.2017.10.260
- Meli E., Pugi L. Preliminary development, simulation and validation of a weigh in motion system for railway vehicles. Meccanica, 2013, vol. 48, no. 10, pp. 2541–2565. https://doi.org/10.1007/s11012-013-9769-9
- Zhou W., Abdulhakeem S., Fang C., Han T., Li G., Wu Y., Faisal Y. A new wayside method for measuring and evaluating wheel-rail contact forces and positions. Measurement, 2020, vol. 166, pp. 108244. https://doi.org/10.1016/j.measurement.2020.108244
- Delprete C., Rosso C. An easy instrument and a methodology for the monitoring and the diagnosis of a rail. Mechanical Systems and Signal Processing, 2009, vol. 23, no. 3, pp. 940–956. https://doi.org/10.1016/j.ymssp.2008.06.004
- Sekuła K., Kołakowski P. Piezo-based weigh-in-motion system for the railway transport. Structural Control Health Monitoring, 2012, vol. 19, no. 2, pp. 199–215. https://doi.org/10.1002/stc.416
- Filograno M.L., Guillén P.C., Rodríguez-Barrios A., Martín-López S., Rodríguez-Plaza M., Andrés-Alguacil A., González-Herráez M. Real-time monitoring of railway traffic using fiber Bragg grating sensors. IEEE Sensors Journal, 2012, vol. 12, no. 1, pp. 85–92. https://doi.org/10.1109/JSEN.2011.2135848
- Kouroussis G., Kinet D., Moeyaert V., Dupuy J., Caucheteur C. Railway structure monitoring solutions using fibre Bragg grating sensors. International Journal of Rail Transportation, 2016, vol. 4, no. 3, pp. 135–150. https://doi.org/10.1080/23248378.2016.1184598
- Roveri N., Carcaterra A., Sestieri A. Real-time monitoring of railway infrastructures using fibre Bragg grating sensors. Mechanical Systems and Signal Processing, 2015, vol. 60–61, pp. 14–28. https://doi.org/10.1016/j.ymssp.2015.01.003
- Johansson A., Nielsen J.C.O. Out-of-round railway wheels-wheel-rail contact forces and track response derived from field tests and numerical simulations. Proceedings of the Institution of Mechanical Engineers, Part F: Journal of Rail and Rapid Transit, 2003, vol. 217, no. 2, pp. 135–145. https://doi.org/10.1243/095440903765762878
- Vendittozzi C., Ciro E., Felli F., Lupi C., Marra F., Pulci G., Astri A. Static and dynamic weighing of rolling stocks by mean of a customized FBG-sensorized-patch. International Journal of Safety and Security Engineering, 2020, vol. 10, no. 1, pp. 83–88. https://doi.org/10.18280/ijsse.100111
- Ereiz S., Duvnjak I., Jiménez-Alonso J.F. Review of finite element model updating methods for structural applications. Structures, 2022, vol. 41, pp. 684–723. https://doi.org/10.1016/j.istruc.2022.05.041
- Chirende B., Li J.Q., Vheremu W. Application of finite element analysis in modeling of bionic harrowing discs. Biomimetics, 2019, vol. 4, no. 3, pp. 61. https://doi.org/10.3390/biomimetics4030061
- Baggio C., Sabbatini V., Santini S., Sebastiani C. Comparison of different finite element model updates based on experimental onsite testing: the case study of San Giovanni in Macerata. Journal of Civil Structural Health Monitoring, 2021, vol. 11, no. 3, pp. 767–790. https://doi.org/10.1007/s13349-021-00480-1
- Denisenko M.A., Isaeva A.S., Sinyukin A.S., Kovalev A.V. A method for measuring the mass of a railroad car using an artificial neural network. Infrastructures, 2024, vol. 9, no. 2, pp. 31. https://doi.org/10.3390/infrastructures9020031