Menu
Publications
2025
2024
2023
2022
2021
2020
2019
2018
2017
2016
2015
2014
2013
2012
2011
2010
2009
2008
2007
2006
2005
2004
2003
2002
2001
Editor-in-Chief
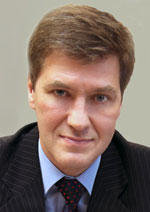
Nikiforov
Vladimir O.
D.Sc., Prof.
Partners
doi: 10.17586/2226-1494-2015-15-4-701-707
DATA TRANSLATION BETWEEN PADS AND CAM350
Read the full article

Article in Russian
For citation: Romanova E.B., Trifonova T. A. Data translation between PADS and CAM350. Scientific and Technical Journal of Information Technologies, Mechanics and Optics, 2015, vol.15, no. 4, pp. 701–707.
Abstract
For citation: Romanova E.B., Trifonova T. A. Data translation between PADS and CAM350. Scientific and Technical Journal of Information Technologies, Mechanics and Optics, 2015, vol.15, no. 4, pp. 701–707.
Abstract
The subject matter of the paper is the process of data translation between computer-aided design system for electronic devices PADS VX and system for technological preparation of production of printed circuit boards CAM350 10. The object of this study is two-way translation of data in these systems. Experimental researches are applied as research methods based on repeated playback of forward and reverse data translation process between PADS and CAM350 systems. The aim is to examine the challenges of data exchange between systems and to find out the ways of their solution. The basis of the work is functionality analysis of PADS and CAM350 systems while data translation, which was carried out in the course of operating experience of these systems. The paper presents advantages and disadvantages of translation methods and their comparison. Errors arising in the process are analyzed. Possible reasons of errors origination are described. The main results are recommendations for data exchange between PADS and CAM350 systems. The proposed recommendations give the possibility to optimize the exchange of data between these systems. Practical significance of the work lies in the implementation of results at LLC «Abeo». Recommendations have been used in the development of dozens of different electronic devices. The use of these results made it possible to reduce the production run-up time, to increase data transmission correctness, thereby improving the quality of products and reduction of their cost.
Keywords: production run-up, printed circuit boards, PADS, CAM350, end-to-end design.
References
References
1. Dilip Save Y., Rakhi R., Shambhulingayya N.D., Srivastava A., Das M.R., Choudhary S., Moudgalya K.M. Oscad: An open source EDA tool for circuit design, simulation, analysis and PCB design. Proc. IEEE
International Conference on Electronics, Circuits, and Systems. Abu Dhabi, United Arab Emirates, 2013, art. 6815548, pp. 851–854. doi: 10.1109/ICECS.2013.6815548
2. Electronic Design Automation. Eds. Laung-Terng Wang, Yao-Wen Chang, Kwang-Ting (Tim) Cheng. Morgan Caufman, 2009, 934 p.
3. Sauerwald M., Pattavina J.S. Printed circuit board (PCB) design issues. In Analog Devices. 1998. 97 p.
4. Kolesnikova T. Marshrut proektirovaniya Mentor Graphics Expedition Enterprise [Route design Mentor Graphics Expedition Enterprise]. Tekhnologii v Elektronnoi Promyshlennosti, 2014, no. 5, pp. 15–21.
5. Kolesnikova T. Proektirovanie printsipial'nykh skhem i pechatnykh plat s pomoshch'yu SAPR Mentor Graphics PADS 9.5 [Design schematics and PCBs using CAD Mentor Graphics PADS 9.5]. Sovremennaya Elektronika, 2014, no. 1, pp. 66–71.
6. Son S., Na S., Kim K., Lee S. Collaborative design environment between ECAD and MCAD engineers in high-tech products development. International Journal of Production Research, 2014, vol. 52, no. 20, pp. 6161–6174. doi: 10.1080/00207543.2014.918289
7. Dankovic D., Vracar L., Prijic A., Prijic Z. An electromechanical approach to a printed circuit board design course. IEEE Transactions on Education, 2013, vol. 56, no. 4, pp. 470–477. doi: 10.1109/TE.2013.2257784
8. Sokolov V. Sekrety raboty v CAM350 [Secrets of work in CAM350]. EDA Expert, 2010, no. 2, pp. 53–57.
9. Moreno-Baez A., Miramontes-de Leon G., Garcia-Domingues E., Sfuentes-Gallardo C. Processing Gerber files for manufacturing printed circuit boards. Procedia Engineering, 2012, vol. 35, pp. 240–244. doi: 10.1016/j.proeng.2012.04.186
10. Oh H.-W., Jung J.-H., Park T.-H. Gerber-character recognition system of autoteaching program for PCB assembly machines. Proc. SICE Annual Conference, 2004, art. FAI-15-4, pp. 1773–1778.
11. Bhavya M., Roy U.M. Design and implementation of position controller for electro hydraulic drives in turbine control system. Proc. IEEE International Conference on Signal Processing, Computing and Control, ISPCC 2013. Shimla, India, 2013, art. 6663463. doi: 10.1109/ISPCC.2013.6663463
12. Ramesh Kumar K.R. Computer-aided design of MIC layout with postprocessor for photoplotter. Defence Science Journal, 1994, vol. 44, no. 4, pp. 317–321.
13. Randelovic S., Zivanovic S. CAD-CAM data transfer as a part of product life cycle. Facta Universitatis. Series: Mechanical Engineering, 2007, vol. 5, no. 1, pp. 87–96.
14. Li J., Han S., Shin S., Lee S., Kang Y., Cho H., Kim H., Song I., Kim I., Singh Rathore P. CAD data exchange using the macro-parametrics approach: an error report. International Journal of CAD/CAM, 2010, vol. 10, no. 2, pp. 53–58.
15. Choi G.-H., Mun D., Han S. Exchange of CAD part models based on the macro-parametric approach. International Journal of CAD/CAM, 2002, vol. 2, no. 1, pp. 13–21.
16. Hoimyr N.-J. CAD/CAM and exchange of product data. Proc. 19th CERN School of Computing. Egmond aan Zee, The Netherlands, 1996, vol. 8, pp. 147–152.
17. Janowski D. Transferring CAD/CAM files. 1999. Available at: http://www.mmsonline.com/articles/transferring-cadcam-files (accessed 23.03.2015).
18. Song I., Han S. Implementation of the direct integration from CAM to CAE for the PCB simulation. Computers in Industry, 2013, vol. 64, no. 8, pp. 1014–1021. doi: 10.1016/j.compind.2013.06.014
19. PADS ES Suite Evaluation Guide. Mentor Graphics Corporation, 2011, 223 p.