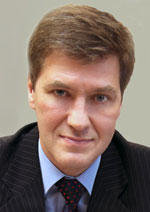
Nikiforov
Vladimir O.
D.Sc., Prof.
doi: 10.17586/2226-1494-2016-16-1-39-45
APPROACH TO AUTOMATION OF LENS COMPONENTS CENTERING FOR ASSEMBLING OF DIFFERENT DESIGN OBJECTIVES
Read the full article

For citation: Pimenov A.Yu. Approach to automation of lens components centering for assembling of different design objectives. Scientific and Technical Journal of Information Technologies, Mechanics and Optics, 2016, vol. 16, no. 1, pp. 39–45.
Abstract
Subject of Research.Existing adjustment methods of lens objectives in two mechanical designs have been analyzed, the main ways of centering error compensation have been considered. The algorithm of automated search of optical elements position has been developed based on the existing methods of centering for compensation of residual decentering. The methods of joint application of this algorithm and centering machine “Trioptics Opticentric” have been suggested. Method. Centering errors of the objective lens components are measured on the centering machine. Aberrations of optical system are calculated by using the received data of centering errors entered to the objective mathematical model. For the calculation of aberration compensation, iteration algorithm of searching of optical elements optimal position is used. The image quality is analyzed for each obtained realization of the optical system. The result of program performance is data matrix about optical components location such that compensation of residual aberrations occurs. Based on the obtained information the system assembling is carried out with the use of centering machine “Trioptics Opticentric”. Main Results. Computer modeling of centering errors for 100 lens apochromatic objectives of drop-in mountings lens design has been carried out. The coma of object axial point image has been chosen as quality estimation criterion. The developed algorithm has been applied for the worst realization of the optical system. In this case the value of integral coma of object axial point image has been decreased by two orders and reduced practically to zero. It is noted that the modeling of adjustment process via using the algorithm of automated search enables to predict the possibility of objective assembly with required quality parameters. Practical Relevance. The received results can be applied on the lines of automated assembly of modern lens objectives.
Acknowledgements. Considerable part of research results was received by Professor Alexander P. Smirnov, untimely passed away.
References
1. Krynin L.I. Osnovy Proektirovaniya Konstruktsii Ob"ektivov [Basis of Lenses Structural Design]. St. Petersburg, SPbGU ITMO Publ., 2006, 254 p.
2. Latyev S.M. Konstruirovanie Tochnykh (Opticheskikh) Priborov [Construction of precise (Optical) Devices]. St. Petersburg, Politekhnika Publ., 2007, 579 p.
3. Latyev S.M., Jablotschnikov E.I., Padun B.S. et al. Laborotory for automated assembly of microscope lenses. Proc. 53 Int. Wissenschaftliches Kolloquium. Techn. Univ. Ilmenau, 2008.
4. Latyev S.M., Smirnov A.P., Voronin A.A., Padun B.S., Yablochnikov E.I., Frolov D.N., Tabachkov A.G., Theska R., Zocher P. The concept of an automatic assembly line for microscope objectives, based on adaptive selection of their components. Journal of Optical Technology, 2009, vol. 76, no. 7, pp. 436–439.
5. Efremov A.A., Zakonnikov V.P., Podobryanskii A.V. Sborka Opticheskikh Priborov [Assembling of Optical Devices]. Moscow, Vysshaya Shkola Publ., 1978, 296 p.
6. Test of camera modules, autocollimator, MTF system - TRIOPTICS. Available at: http://www.trioptics.com (accessed 15.09.2015).
7. Smirnov A.P. Model of the optical system in medium MathCad. Journal of Instrument Engineering, 2007, vol. 50, no. 4, pp. 56–62.
8. Smirnov A.P., Pimenov A.Yu., Abramov. D.A. Modelirovanie linzovykh opticheskikh sistem v srede Mathcad. Sbornik Trudov X Mezhdunarodnoi Konferentsii Prikladnaya optika 2012 [Proc. X Int. Conf. on Applied Optics 2012]. St. Petersburg, 2012, vol. 3, pp. 75–79.
9. Smirnov A.P., Abramov. D.A., Pimenov A.Yu. Komp'yuternoe Modelirovanie Opticheskikh Sistem. Chast' 1. Linzovye Ustroistva. Praktikum v Srede MathCad [Computer Modeling of Optical Systems. Part 1: Lens Devices. Practice in MathCad]. St. Petersburg, NIU ITMO Publ., 2012, 84 p.
10. Vukobratovich D., Valente T.M., Shannon R.R., Hooker R., Sumner R.E. Optomechanical Systems Design. In The Infrared and Electro Optical Systems Handbook, vol. 4. Bellingham, SPIE Optical Engineering Press, 1993.
11. Bacich J.J. Precision Lens Mounting. Patent US 4733945, 1988.
12. Yoder P.R. Mounting Optics in Optical Instruments. 2nd ed. Washington, SPIE Press Bellinham, 2008, 782 p.
13. Hopkins R.E. Applied Optics and Optical Engineering. Vol. VIII. New York, Academic Press, 1980.
14. Latyev S.M., Rumyantsev D.M., Kuritsyn P.A. Design and process methods of centering lens systems. Journal of Optical Technology, 2013, vol. 80, no. 3, pp. 197–200. doi: 10.1364/JOT.80.000197
15. Buy D., Beloyvan P.A., Latyev S.M., Tabachkov A.G. Alignment of poker-chips objectives. Sovremennye Problemy Nauki i Obrazovaniya, 2015, no. 1, p. 108.
16. Latyev S.M., Buj D.B., Tregub V.P. Method for Centring Lens in Holder and Holder Therefor. Patent RU2542636, 2015.
17. Alekseeva N.N., Krynin L.I., Lapo L.M., Pimenov Yu.D., Sokol'skii M.N., Frolov D.N., Tabachkov A.G. Apokhromaticheskii Ob"ektiv [Apochromatic Lens]. Patent RU32612, 2003.
18. Smirnov A.P., Latyev S.M., Markov D.V., Chugunov S.A. Comparative analysis of tolerances on microlens primary errors by Monte Carlo method. Journal of Instrument Engineering, 2012, vol. 55, no. 4, pp. 82–87.