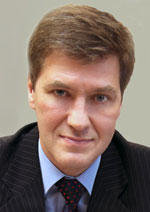
Nikiforov
Vladimir O.
D.Sc., Prof.
doi: 10.17586/2226-1494-2016-16-2-303-310
DEVELOPMENT AND TESTING OF ERRORS CORRECTION ALGORITHM IN ELECTRONIC DESIGN AUTOMATION
Read the full article

For citation: Romanova E.B. Development and testing of errors correction algorithm in electronic design automation. Scientific and Technical Journal of Information Technologies, Mechanics and Optics, 2016, vol. 16, no. 2, pp. 303–310. doi:10.17586/2226-1494-2016-16-2-303-310
Abstract
Subject of Research. We have developed and presented a method of design errors correction for printed circuit boards (PCB) in electronic design automation (EDA). Control of process parameters of PCB in EDA is carried out by means of Design Rule Check (DRC) program. The DRC program monitors compliance with the design rules (minimum width of the conductors and gaps, the parameters of pads and via-holes, the parameters of polygons, etc.) and also checks the route tracing, short circuits, the presence of objects outside PCB edge and other design errors. The result of the DRC program running is the generated error report. For quality production of circuit boards DRC-errors should be corrected, that is ensured by the creation of error-free DRC report. Method. A problem of correction repeatability of DRC-errors was identified as a result of trial operation of P-CAD, Altium Designer and KiCAD programs. For its solution the analysis of DRC-errors was carried out; the methods of their correction were studied. DRC-errors were proposed to be clustered. Groups of errors include the types of errors, which correction sequence has no impact on the correction time. The algorithm for correction of DRC-errors is proposed. Main Results. The best correction sequence of DRC-errors has been determined. The algorithm has been tested in the following EDA: P-CAD, Altium Designer and KiCAD. Testing has been carried out on two and four-layer test PCB (digital and analog). Comparison of DRC-errors correction time with the algorithm application to the same time without it has been done. It has been shown that time saved for the DRC-errors correction increases with the number of error types up to 3.7 times. Practical Relevance. The proposed algorithm application will reduce PCB design time and improve the quality of the PCB design. We recommend using the developed algorithm when the number of error types is equal to four or more. The proposed algorithm can be used in different types of modern EDA.
Acknowledgements. The author thanks Sergey Arustamov, Professor of Computer Systems Design and Security Department (ITMO University), for critical remarks and advice that have improved significantly the quality of this paper.
References
1. Zhang L., Peng X.F., He L., Wan W.L. Complete design of circuit board based on Altium Desinger summer 09. Applied Mechanics and Materials, 2013, vol. 423–426, pp. 2679–2683. doi: 10.4028/www.scientific.net/AMM.423-426.2679
2. Wu T., Wang S.-X. Application of EDA technology in the education of automatic control system design. Communications in Computer and Information Science, 2011, vol. 218, no. 5, pp. 240–244. doi: 10.1007/978-3-642-23357-9_43
3. Dilip Save Y., Rakhi R., Shambhulingayya N.D., Srivastava A., Das M.R., Choudhary S., Moudgalya K.M. Oscad: an open source EDA tool for circuit design, simulation, analysis and PCB design. Proc. 20th Int. Conf. on Electronics, Circuits, and Systems, 2013, pp. 851–854. doi: 10.1109/ICECS.2013.6815548
4. Zhai X.J., Bensaali F. Improved number plate character segmentation algorithm and its efficient FPGA implementation. Journal of Real-Time Image Processing, 2015, vol. 10, no. 1, pp. 91–103. doi: 10.1007/s11554-012-0258-5
5. O'Riordan D. Capturing and applying design intent. Electronic Engineering Times, 2006, no. 8, pp.
1435–1444.
6. Pais A.P.V., Anido M.L., Oliveira C.E.T. Developing a distributed architecture for design rule checking. Proc. 44th IEEE 2001 Midwest Symposium on Circuits and Systems. Dayton, OH, 2001, vol. 2, pp. 678–681. doi: 10.1109/MWSCAS.2001.986279
7. Page T. Implementation of sample design rules in a commercially used PCB design application. Advances in Manufacturing Technology, 2000, vol. XIV, pp. 125–129.
8. Ismail M., El Shamy R.S., Madkour K., Hammouda S., Swillam M.A. Toward new design-rule-check of silicon photonics for automated layout physical verifications. Proceedings of SPIE - The International Society for Optical Engineering, 2015, vol. 9367, art. 93671K. doi: 10.1117/12.2078357
9. Romanova E.B., Sumtsov A.V. Analysis and correction of DRC-errors in EDA system. Journal of Instrument Engineering, 2015, vol. 58, no. 10, pp. 840–846. doi: 10.17586/0021-3454-2015-58-10-840-846
10. Romanova E.B. Import of projects from P-CAD to Altium Designer. Tekhnologii v Elektronnoi Promyshlennosti, 2012, no. 3(55), pp. 18–19.
11. Arustamov S.A., Gatchin Yu.A., Romanova E.B. P-CAD-2006 package functional analysis based on usage experience. Scientific and Technical Journal of Information Technologies, Mechanics and Optics, 2009, no. 1 (59), pp. 114–120.
12. Kuznetsova O.V., Korobeinikov A.G., Romanova E.B. Comparative analysis of P-CAD 2006 and 2012 ALTIUM DESIGNER. Cybernetics and Programming, 2013, no. 6, pp. 17–27. (In Russian)
13. Charras J.P., Tappero F. KiCad. Pcbnew. Available at: http://docs.kicad-pcb.org/en/pcbnew.pdf (accessed 20.09.2015).
14. EAGLE. Manual Version 7. Available at: http://www.cadsoftusa.com/fileadmin/journalist/Documents/V7.3_manual_en.pdf (accessed 20.09.2015).