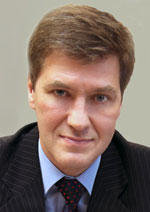
Nikiforov
Vladimir O.
D.Sc., Prof.
doi: 10.17586/2226-1494-2016-16-5-936-945
MATHEMATICAL AND COMPUTER MODELING OF AUTOMATIC CONTROL SYSTEM FOR HYDROSTATIC BEARING
Read the full article

For citation: Pelevin N.A., Prokopenko V.A., Chernov I.A. Mathematical and computer modeling of automatic control system for hydrostatic bearing. Scientific and Technical Journal of Information Technologies, Mechanics and Optics, 2016, vol. 16, no. 5, pp. 936–945. doi: 10.17586/2226-1494-2016-16-5-936-945
Abstract
The paper presents simulation results of hydrostatic bearing dynamics in spindle assembly of standard flexible production module with throttled circuit. The necessity of dynamic quality increase for automatic control system of the hydrostatic bearing with the use of correcting means in the form of RC-chains is shown. The features of correction parameters choice coming from the existence of the crossing connections in automatic control system structure are noted. We propose the block diagram of automatic control system of the hydrostatic bearing in Simulink working field and cyclic algorithm for determination program of RC-chain parameters implemented in MATLAB taking into account typical thermal processes for the finishing treatment. Graphic-analytical method for the correction parameters choice is presented based on the stability stock phase gradient for dynamic quality determination of automatic control system. Researches of the method estimability in case of using the standard metal bellow valve as the hydrocapacity for RC-chain are also carried out. Recommendations for the bellow valve choice are formulated. The check of dynamic quality indicators concerning transition processes calculated by means of the appropriate programs developed for MATLAB is performed. Examples are given for phase stability factor gradient schedules with partition of various areas of hydrostatic bearing dynamic quality for different frequencies of spindle rotation and procedure description of data cursor function application on MATLAB toolbar. Improvement of hydrostatic bearing dynamics under typical low loadings for finishing treatment is noted. Also, decrease of dynamic indicators for high loadings treatment in case of roughing treatment is marked.
References
1. Ramamurti V., Kumar K.E.M. Machine tool dynamics - a review. Proc. Indian natn. Sci. Acad., 1996, vol. 62, no. 2, pp. 125–136.
2. Voll H. Abrenzung der Andwendunf von Walzlagerungen gegenuber anderen Lagersystemen. FAG, publ. no. 02113 DA, 1984, pp. 48¬–56.
3. Molodtsov V.V., Churilin A.V., Bushuev V.V. High-speed spindle bearings for modern machines. Vestnik of MSTU Stankin, 2014, no. 4, pp. 85–97.
4. Mohsin M.E., Morsi S.A. The dynamic stiffness of controlled hydrostatic bearings. Journal of Lubrication Technology, 1969, vol. 91, no. 4, pp. 597–608.
5. Przybyl R. Some aspects of application of the hydrostatic bearings in machine tools. Mechanics and Mechanical Engineering, 2008, vol. 12, no. 3, pp. 243–253.
6. Rothenhofer G., Slocum A., Yui A. Design, dynamic modeling, simulation and feedback control of a hydrostatic thrust bearing. Proc. 10th Int. Conf. of the European Society for Precision Engineering and Nanotechnology, EUSPEN 2008. Zurich, Switzerland, 2008, pp. 509–513.
7. Bassani R., Piccigallo B. Hydrostatic Lubrication. Amsterdam, Elsevier, 1992, 541 p.
8. Stansfield M.F. Hydrostatic Bearings for Machine Tools and Similar Applications. Machinery Publishing, 1970, 227 p.
9. Privalov V.V., Privalova O.V., Prokopenko V.A., Skubov D.Ju. Simulation and nonlinear analysis of the dynamic properties of hydrostatic bearing systems. In: 44IWK99. Ilmenau, TUI, 1999, pp. 273–278.
10. Hesselbach J., Abel-Keilhack C. Active hydrostatic bearing with magnetorheological fluid. Journal of Applied Physics, 2003, vol. 93, no. 10, pp. 8441–8443. doi: 10.1063/1.1555850
11. Bushuev V.V., Kuznetsov A.P., Sabirov F.S., Khomyakov V.S., Molodtsov V.V. Trends in research on metal-cutting machines. Russian Engineering Research, 2016, vol. 36, no. 6, pp. 488–495. doi: 10.3103/S1068798X16060083
12. Bhushan B. Principles and Applications of Tribology. NY, Wiley, 2013, 1006 p.
13. Rowe W.B., Cheng K. Hypermedia as a design tool with application to design of fluid film journal bearings. CIRP Annals - Manufacturing Technology, 1992, vol. 41, no. 1, pp. 209–212. doi: 10.1016/S0007-8506(07)61187-1
14. Favareto M, Razelli G. Design and testing of universal hydrostatic boring spindle. Extern. Pressur. Bearings, London, 1972, pp. 309–316.
15. Bundur M.S., Pelevin N.A., Prokopenko V.A. Dynamic simulation of hydrostatic bearings using MATLAB Simulink framework. Proc. 4th Int. Science and Practical Conference on Modern Engineering Technology, Science and Education. St. Petersburg, SPbSPU Publ., 2014, pp. 815–825.
16. Kondrashov V.E., Korolev S.B. MATLAB kak Sistema Programmirovaniya Nauchno-Tekhnicheskikh Raschetov [MATLAB as a Programming System of Scientific and Technical Calculations]. Moscow, Mir, 2002, 352 p.
17. Borisevich A.V. Teoriya Avtomaticheskogo Upravleniya: Elementarnoe Vvedenie s Primeneniem MATLAB [Automatic Control Theory: An Elementary Introduction using MATLAB]. Moscow, Infra-M Publ., 2014, 200 p.
18. Pelevin N.A. Computer modeling of energy processes in the hydrostatic bearing spindle. Proc. Int. Conf. on Computer Modeling, COMOD-2015. St. Petersburg, 2015, pp. 74–82. (In Russian)
19. Bundur M.S., Pelevin N.A., Prokopenko V.A. Features of dynamics of hydrostatic head slides bearings of technological equipment. Proc. ХII Int. Conf. on Dynamics of Technical Systems. Rostov-on-Don, Russia, 2015, pp. 300–304. (In Russian)
20. Bundur M.S., Prokopenko V.A., Chernov I.A. Modeling and improving the dynamic characteristics of spindle units based on hydrostatic bearings. Scientific and Technical Journal of Information Technologies, Mechanics and Optics, 2009, no. 6, pp. 32–37. (In Russian)
21. Bundur M.S., Prokopenko V.A., Chernov I.A. Metal-Cutting Equipment. Design of Hydrostatic Bearings. Practical guidelines. St. Petersburg, SPbSPU Publ., 2009, 28 p. (In Russian)
22. Ivashchenko N.N. Avtomaticheskoe Regulirovanie. Teoriya i Elementy Sistem [Automatic Control. Theory and System Elements Build-up]. Moscow, Mashinostroenie Publ., 1983, 608 p.
23. Bundur M.S., Prokopenko V.A., Pelevin N.A. Fore-casting of dynamic quality of spindle hydrostatic bearings at the consideration of energy processes. Metalloobrabotka, 2016, no. 2, pp. 56–63. (In Russian)