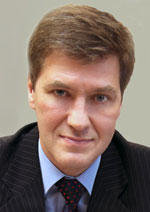
Nikiforov
Vladimir O.
D.Sc., Prof.
doi: 10.17586/2226-1494-2017-17-5-910-919
SIMULATION OF CENTRIFUGAL PUMP IMPELLER WITH MAXIMUM CAVITATION EFFECT
Read the full article

For citation: Ukolov A.I., Rodionov V.P., Starovoytov P.P. Simulation of centrifugal pump impeller with maximum cavitation effect. Scientific and Technical Journal of Information Technologies, Mechanics and Optics, 2017, vol. 17, no. 5, pp. 910–919 (in Russian). doi: 10.17586/2226-1494-2017-17-5-910-919
Abstract
Subject of Research. We consider the possibility of cavitation phenomenon stimulating in blade machines for the purpose of the pumped liquid processing. The paper presents numerical analysis of geometry influence of the motor centrifugal pump on the cavitation cavity formation in the inter blade space of its impeller. Methods. We usethe capabilities of the ANSYS Workbench software package for finite element analysis and the integrated module ANSYS CFX for optimizing the process of development and technological preparation in the field of computational dynamics of liquids and gases. Main Results.The impeller design for a motor centrifugal pump has been developed with characteristics similar to this type of device. The constructed geometric model is compact in size, has the right pressure distribution in the impeller cross section and is not subjected to cavitation at a given operating mode. It is shown that cavitation occurs at the anterior edge of the blade with a relative increase in the outer radius of the impeller or a decrease in its width within the range of 12-50% in comparison with a model close to the necessary for stable operation, and it is followed by the growth throughout the volume of the flowing part of the pump. Practical Relevance. This kind of pump can be used as a hydrodynamic machine to intensify many chemical and technological processes due to cavitation effect, as early as the stage of the liquid pumping.
References
1. Rodionov V.P. Jet Super Cavitation Erosion. Krasnodar, KubGTU Publ., 2005, 223 p. (In Russian)
2. Haworth K. J., Raymond J. L., Radhakrishnan K. et al. Trans-stent B-mode ultrasound and passive cavitation imaging. Ultrasound in Medicine and Biology, 2016, vol. 42, no 2, pp. 518–527. doi: 10.1016/j.ultrasmedbio.2015.08.014
3. Zarnitsyn V., Rostad C. A., Prausnitz M. R. Modeling transmembrane transport through cell membrane wounds created by acoustic cavitation. Biophysical Journal, 2008, vol. 95, no. 9, pp. 4124–4138. doi: 10.1529/biophysj.108.131664
4. Sinden D. Modelling cavitation in liver tissue under high-intensity focused ultrasound. British Applied Mathematics Colloquium. Birmingham, 2011.
5. Promtov M.A. Prospects of cavitation technologies application for intensification of chemical technological processes. Transactions of the TSTU, 2008, vol. 14, no. 4, pp. 861–869. (In Russian)
6. Sheng H.-Z., Zhang Z.-P., Wu C.-K. Study of atomization and micro-explosion of water-in-diesel fuel emulsion droplets in spray within a high temperature, high pressure bomb. International Symposium COMODIA, 1990, pp. 275–280.
7. Seifi M.R., Hassan-Beygi S.R., Ghobadian B., Desideri U., Antonelli M. Experimental investigation of a diesel engine power, torque and noise emission using water-diesel emulsions. Fuel, 2016, vol. 166, no 15. pp. 392–399. doi: 10.1016/j.fuel.2015.10.122
8. Fahd M.E.A., Wenming Y., Lee P.S., Chou S.K., Yap C.R. Experimental investigation of the performance and emission characteristics of direct injection diesel engine by water emulsion diesel under varying engine load condition. Applied Energy, 2013, vol. 102, pp. 1042–1049. doi: 10.1016/j.apenergy.2012.06.041
9. Spiridonov E.K. Characteristics and Calculation of Cavitation Mixers. Procedia Engineering, 2015, vol. 129, pp. 446–450. doi: 10.1016/j.proeng.2015.12.148.
10. Kulagin V.A. Grishchenko E.P. Hydro and Gas Dynamics: Textbook. Krasnoyarsk, IPK SFU Publ., 2009, 278 p. (In Russian)
11. Cehovin M., Medic A., Scheideler J. et al. Hydrodynamic cavitation in combination with the ozone, hydrogen peroxide and the UV-based advanced oxidation processes for the removal of natural organic matter from drinking water. Ultrasonics Sonochemistry, 2017, vol. 37, pp. 394–404. doi: 10.1016/j.ultsonch.2017.01.036
12. Mishra K.P., Gogate P.R. Intensification of degradation of Rhodamine B using hydrodynamic cavitation in the presence of additives. Separation and Purification Technology, 2010, vol. 75, no. 3, pp. 385–391. doi: 10.1016/j.seppur.2010.09.008
13. Sarc A., Stepisnik-Perdih T., Petkovsek M., Dular M. The issue of cavitation number value in studies of water treatment by hydrodynamic cavitation. Ultrasonics Sonochemistry, 2017, vol. 34, pp. 51–59. doi: 10.1016/j.ultsonch.2016.05.020.
14. Joshi R.K., Gogate P.R. Degradation of dichlorvos using hydrodynamic cavitation based treatment strategies. Ultrasonics Sonochemistry, 2012, vol. 19, no. 3, pp. 532–539. doi: 10.1016/j.ultsonch.2011.11.005
15. Petkovsek M., Zupanc M., Dular M. et al. Rotation generator of hydrodynamic cavitation for water treatment. Separation and Purification Technology, 2013, vol. 118, no. 3, pp. 415–423. doi: 10.1016/j.seppur.2013.07.029
16. Petkovsek M., Mlakar M., Levstek M. et. al. A novel rotation generator of hydrodynamic cavitation for waste-activated sludge disintegration. Ultrasonics Sonochemistry, 2015, vol. 26, pp. 408–414. doi: 10.1016/j.ultsonch.2015.01.006
17. Valyuhov S.G., Kretinin A.V., Galdin D.N., Baranov S.S. Optimising design of the flowing part of the main oil pump with use of TURBO of the ANSYS tools. Pumps. Turbines. Systems, 2015, vol. 14, no. 1, pp. 56–68. (In Russian)
18. ANSYS CFX. Computer simulation helps design more efficient water pumps. World Pumps, 2004, no. 453, pp. 32–34. doi: 10.1016/S0262-1762(04)00228-7
19. Tsutsumi K., Watanabe S., Tsuda S., Yamaguchi T. Cavitation simulation of automotive torque converter using a homogeneous cavitation model. European Journal of Mechanics - B/Fluids, 2017, vol. 61, part 2, pp. 263–270. doi: 10.1016/j.euromechflu.2016.09.001
20. Aleksensky V.A., Zharkovsky A.A., Pugachev P.V. Calculation definition of centrifugal pumps cavitational characteristics. Proceedings of the Samara Scientific Center of the Russian Academy of Sciences, 2011, vol. 13, no. 1-2, pp. 411–414. (In Russian)
21. Alekseev D.P., Kuzmin A.V., Chulyunin A.Yu. Numerical simulation of cavitation in centrifugal pump. International Research Journal, 2014, vol. 24, no. 5, pp. 121–125. (In Russian)
22. Wursthorn S. Numerische Untersuchung kavitierender Stromungen in einer Modellkreiselpumpe. Karlsruhe, 2001, 185 p.
23. Chen Y., Heister S.D. Two-phase modeling of cavitated flows. Computers & Fluids, 1995, vol. 24, no. 7, pp. 799–809. doi: 10.1016/0045-7930(95)00017-7
24. Konstantinov S.Yu. Methods of Analytical and Numerical Calculation of Hydraulic Characteristics and Design Parameters of Jet-Cavitational Flow Stabilizer. Dis. PhD Eng. Sci. Ufa, 2015, 131 p. (In Russian)
25. Smorodov E.A., Galiahmetov R.N., Il'gamov M.A. Physics and Chemistry of Cavitation. Moscow, Nauka Publ., 2008, 226 p. (In Russian)
26. Bashta T.M., Rudnev S.S., Nekrasov B.B. et. al. Hydraulics, Hydraulic Machines and Hydraulic Drives. Moscow, Mashinostroenie Publ., 1982, 423 p. (In Russian)
27. Askew J.R. Centrifugal pumps: avoiding cavitation. World Pumps, 2011, no. 7-8. pp. 34–39. doi: 10.1016/S0262-1762(11)70207-3