Menu
Publications
2025
2024
2023
2022
2021
2020
2019
2018
2017
2016
2015
2014
2013
2012
2011
2010
2009
2008
2007
2006
2005
2004
2003
2002
2001
Editor-in-Chief
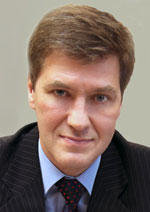
Nikiforov
Vladimir O.
D.Sc., Prof.
Partners
doi: 10.17586/2226-1494-2017-17-6-1123-1132
SPECIAL DESIGN ASPECTS OF GRIPPING DEVICES FOR INCREASING THE FLEXIBILITY OF AUTOMATED AND ROBOTIC MANUFACTURING LINES AT INSTRUMENT MANUFACTURING FACILITIES
Read the full article

Article in Russian
For citation: Medunetskiy V.M., Padun B.S., Nikolaev V.V. Special design aspects of gripping devices for increasing the flexibility of automated and robotic manufacturing lines at instrument manufacturing facilities. Scientific and Technical Journal of Information Technologies, Mechanics and Optics , 2017, vol. 17, no. 6, pp. 1123–1132 (in Russian). doi: 10.17586/2226-1494-2017-17-6-1123-1132
Abstract
For citation: Medunetskiy V.M., Padun B.S., Nikolaev V.V. Special design aspects of gripping devices for increasing the flexibility of automated and robotic manufacturing lines at instrument manufacturing facilities. Scientific and Technical Journal of Information Technologies, Mechanics and Optics , 2017, vol. 17, no. 6, pp. 1123–1132 (in Russian). doi: 10.17586/2226-1494-2017-17-6-1123-1132
Abstract
The paper deals with the tasks of increasing manufacturing flexibility of automated production lines on the example of microlens assembly automation. Consideration was given to peculiarities of building an automated microlens assembly line and to specifications of the basic microlens design. Weight and dimensional parameters of the basic microlens main units were analyzed and systematized. It was noted that the range of items produced by the automated line and its manufacturing flexibility are substantially influenced by the design of universal arm grippers interoperating with microlens parts and assemblies in the process of automated assembly that gives the possibility to cover an entire range of microlenses. Designs of known industrial grippers were reviewed and an analysis was provided as to the possibility of their application for the automated microlens assembly line. The analysis resulted in two alternative schemes proposed for building a universal gripper. A developed and proved out methodology of qualitative-quantitative assessment of technical solutions was used. This methodology is intended for mechanical system developers, who make a justified choice of technical solutions from a variety of alternatives, and is aimed to raise the quality level of technical products being designed that are introduced at the design stages. Following the presented methodology, the qualitative-quantitative assessment of two proposed gripper variants was carried out, and the third universal gripper construction variant was put forward based on its analysis. Specific universal gripper design for an automated microlens assembly line was proposed.
Keywords: automated microlens assembly, manufacturing flexibility increase, universal gripper, technical solutions comparison
References
References
1. Kutergin V.A. World trends in the development of intellectual or "smart" industries and enterprises. URL: www.umpro.ru/index.php?art_id_1=545&group_id_4=26&page_id=17 (accessed: 10.04.2017).
2. Industrial Development Report 2016. The Role of Technology and Innovation in Inclusive and Sustainable Industrial Development. Vienna, 2016, 286 p.
3. Mitrofanov S.P., Kulikov D.D., Milyaev O.N., Padun B.S. Technological Background of Flexible Production Systems. Leningrad, Mashinostroenie Publ., 1987, 352 p. (In Russian)
4. Mitrofanov S.P. Group Technology of Machine-Making. Leningrad, Mashinostroenie Publ., 1983. (In Russian)
5. Tommila T., Hirvonen J., Jaakkola L., Peltoniemi J., Peltola J., Sierla S., Koskinen K. Next generation of industrial automation: Concepts and architecture of a component-based control system. VTT Tiedotteita. Research Notes2303, 104 p.
6. Bondareva N.N. The current state and the perspectives of robotics development: in the global and Russia. MIR [World] (Modernization. Innovation. Research), 2016, vol. 7, no. 3, pp. 49–57. (In Russian) doi: 10.18184/2079-4665.2016.7.3.49.57
7. RossL.T., Fardo S.W., Masterson J., Towers R. Robotics: Theory and Industrial Applications. 2nd ed. Goodheart-Willcox,2011, 317 p.
8. Robo Global Defining the Universe of Robotics & Automation for Investors. URL: http://roboglobal.com/system/pdf_attachments/documents/000/000/299/original/Robo_Global_Presentation_JAN_2017.pdf (accessed: 27.05.2017).
9. Executive Summary World Robotics 2016 Industrial Robots, 2016, pp. 11–18. URL: ifr.org/img/uploads/Executive_Summary_WR_Industrial_Robots_20161.pdf (accessed: 10.06.2017).
10. Bui Dinh Bao, Latyev S.M., Beloivan P.A., Tabachkov A.G. Analysis of lens registration in mounts. Journal of Optical Technology, 2015, vol. 82, no. 12, pp. 792–795. doi: 10.1364/JOT.82.000792
11. Latyev S.M., Bui Dinh Bao, Beloivan P.A., Tabachkov A.G. Analysis of certain issues in the assembly of fast objectives.Journal of Optical Technology, 2015, vol. 82, no. 12, pp. 796–799. doi: 10.1364/JOT.82.000796
12. Latyev S.M., Beloivan P.A. Effect of mounting gaps between components on the centering of lens objectives. Journal of Optical Technology, 2016, vol. 83, no. 12, pp. 738–742. doi: 10.1364/JOT.83.000738
13. Araslanov D.Yu., Tabachkov A.G. Procedure of manufacturing the front parts microobjective. Sovremennye Problemy Nauki i Obrazovaniya, 2015, no. 1-1, p. 263. (In Russian)
14. Tabachkov A.G., Frolov D.N., Latyev S.M. Standardizing the designs of lens microscope objectives. Journal of Optical Technology, 2011, vol. 78, no. 1, pp. 30–34. (In Russian)
15. Latyev S.M., Tabachkov A.G., Frolov D.N., Reznikov A.S. Unification of optical аnd mechanical design of lens microobjectives.Journal of Instrument Engineering, 2011, vol. 54, no. 11, pp. 14–21. (In Russian)
16. Aliev T.I., Padun B.S. Optimization of microlens assembly processes. Journal of Instrument Engineering, 2010, vol. 53, no. 8, pp. 39–46. (In Russian)
17. Padun B.S., Latyev S.M. Integrated system of automated assembly of microlenses. Journal of Instrument Engineering, 2010, vol. 53, no. 8, pp. 34–39. (In Russian)
18. Latyev S.M., Smirnov A.P., Voronin A.A., Padun B.S., Yablochnikov E.I. et al. Concept of automated assembly line of microscop lens based on adaptive selection of their components. Journal of Optical Technology, 2009, vol. 76, no. 7, pp. 436–439. doi: 10.1364/JOT.76.000436
19. Latyev S.M., Smirnov A.P., Tabachkov A.G., Frolov D.N., Shukhat R.V. Design of automated assembly line for microscop lens. Journal of Instrument Engineering, 2011, vol. 54, no. 11, pp. 7–12.
20. AngularAirGripper. Series MHC2/MHCA2/MHCM2. URL: http://www.kampm.ru/pdf/PnevCyl/grip_angle/mhc2.pdf(accessed: 01.06.2017).
21. Air Gripper. Series MHY2. URL: smc138.valuehost.ru/c5/mhy2.pdf(accessed: 05.06.2017).
22. Toggle Style Air Gripper. Series MHT2. URL: www.smclt.lt/failai/MHT2_EU.pdf(accessed: 15.06.2017).
23. 180° Angular Gripper, Rack and Pinion Style. Series MHW2. URL: www.dianas.ru/netcat_files/261/285/h_4d1f77223fdf3aee38950a2185ddb2b4 (accessed: 10.06.2017).
24. Wedge Cam Operation Slide Guide Air Gripper Series MHK2. URL: smc138.valuehost.ru/c5/mhk2.pdf (accessed: 10.06.2017).
25. ParallelGripperSeries MHZ2. URL: smc138.valuehost.ru/c5/mhz2.pdf (accessed: 10.06.2017).
26. AirGripperof Parallel TypeMHS. URL: mk-pnevmocenter.ru/images/pdf/mhs-obzor.pdf (accessed: 10.06.2017).
27. Medunetskiy V.M., Nikolaev V.V. Estimation technique of mechanical products quality level in design process.Scientific and Technical Journal of Information Technologies, Mechanics and Optics, 2016, vol. 16, no. 6, pp. 1128–1132. doi: 10.17586/2226-1494-2016-16-6-1128-1132
28. Keeney R.L., Raiffa H. Decisions with Multiple Objectives: Preferences and Value Tradeoffs. Cambridge University Press, 1993, 592 p.
29. Lisetskiy Yu.M. Method of complex expert evaluation for difficult technical systems planning. Matematicheskie Mashinyi Sistemy, 2006, no. 2, pp. 141–146.
30. Boardman A.E., Greenberg D.H., Vining A.R., Weimer D.L. Cost-Benefit Analysis: Concepts and Practice. 3rd ed. New Jersey, Upper Saddle River, 2006, 560 p.
31. Altshuller G. The Innovation Algorithm: TRIZ, Systematic Innovation, and Technical Creativity. Technical Innovation Center, Worcester, 1999, 312 p.
32. Savransky S.D. Engineering of Creativity: Introduction to TRIZ Methodology of Inventive Problem Solving. Boca Raton, CRC Press, 2000.
33. Kim J.H., Lee J.Y., Kang S.W. The acceleration of TRIZ propagation in Samsung Electronics. Proc. ETRIA TRIZ Future 2005 Conference. Graz, Austria, 2005.