Menu
Publications
2025
2024
2023
2022
2021
2020
2019
2018
2017
2016
2015
2014
2013
2012
2011
2010
2009
2008
2007
2006
2005
2004
2003
2002
2001
Editor-in-Chief
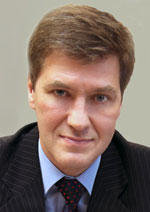
Nikiforov
Vladimir O.
D.Sc., Prof.
Partners
doi: 10.17586/2226-1494-2020-20-2-283-289
MODELING OF WINDING PROCESSOF COMPOSITE CYLINDRICAL SHELLS
Read the full article

Article in Russian
For citation:
Abstract
For citation:
Kutin A.Yu., Aryasov G.P. Modeling of winding process of composite cylindrical shells. Scientific and Technical Journal of Information Technologies, Mechanics and Optics, 2020, vol. 20, no. 2, pp. 283–289 (in Russian). doi: 10.17586/2226-1494-2020-20-2-283-289
Abstract
Subject of Research. The paper presents a review of an effective filament winding method for hollow composite products manufacturing (tubes and containers). Finished products are lightweight, durable and widely used in industry. However, this method has significant drawbacks. The tension of the surface layer and the tension of the inner layers can differ significantly for the formed products. This effect is also observed when the tension of the wound material is regulated. Another significant disadvantage of technology is the change in the cross-sectional diameter of the product in the end zone, where the backward motion of the movable trolley with filaments (tape) is performed. Due to these shortcomings, there are deviations in the winding density and other indicators of the stress-strain state from the planned values. Method. We offer an original method for controlling the radial increment of the composite winding and its density to eliminate mentioned above drawbacks. The method is based on a composite winding model. The model is developed in view of the following representation: the trajectory of the winding-on point is a spiral in a section perpendicular to the axis of the mandrel rotation. The specified winding density, the normalized increment of the winding radius and the change in the angular velocity of the mandrel in the end zones are determined by this model. The model analysis shows that actual speed of the winding point should be equal to the theoretical one for the deterministic winding process. If this condition is met, then all other technological parameters (radius, length, density) will be reproduced on the basis of pre-known functions. It is advisable to maintain the equality between the actual winding radius and theoretical winding radius for the practical implementation of the control algorithm winding process. If this condition is implemented, then the process of material winding will be predictable. Main Results. A control device for the winding process implementing this method is designed. The device provides an action on the winding with variable force, adequately responding to random disturbances and maintaining equality between the actual and calculated winding radii. The Simulink application, an integral part of the Matlab application package, is used for control device modeling. Practical Relevance. The proposed efficient solution for the control composite winding density provides stabilization of the stress-strain state of the cylindrical composite products by changing the radial increment of the winding layers and preventing the effect of the random factors and, consequently, increases production efficiency.
Keywords: composite material, circumferential winding, thread tension, composite winding density control
References
References
-
Quagliano Amado J.C. Manufacture and testing of lightweight tubes for rocketry and centrifuges. Lightweight Composite Structures in Transport: Design, Manufacturing, Analysis and Performance, 2016, pp. 421–437. doi: 10.1016/B978-1-78242-325-6.00017-7
-
Shi Y.Y., Tang H., Yu Q. Key technology of the NC tape-winding machine. Hangkong Xuebao/Acta Aeronautica et Astronautica Sinica, 2008, vol. 29, no. 1, pp. 233–239.
-
Li Z. Tension control system design of a filament winding structure based on fuzzy neural network. Engineering Review, 2015, vol. 35, no. 1, pp. 9–17.
-
Zhang H., Tang H., Shi Y. Precision tension control technology of composite fiber tape winding molding. Journal of Thermoplastic Composite Materials, 2018, vol. 31, no. 7, pp. 925–945. doi: 10.1177/0892705717729018
-
Srivastava S., Shariqul H. A brief theory on latest trend of filament winding machine. International Journal of Advanced Engineering Research and Science, 2016, vol. 3, no. 4, pp. 33–38.
-
Ren S.-L., Lai Y.-N., Wang Y.-Z., Hua L. A new fiber winding precisiong tension control system. Proc. of the IEEE International Conference on Automation and Logistics (ICAL 2009), Shenyang, China, 2009, pp. 233–236. doi: 10.1109/ICAL.2009.5262921
-
Musalimov V.M., Monakhov Yu.S., Kutin A.Yu., Solovieva G.A. Modeling of the process of winding threads on a rigid cylinder. Journal of Instrument Engineering, 2016, vol. 59, no. 8, pp. 657–663. (in Russian). doi: 10.17586/0021-3454-2016-59-8-657-663
-
Lü H., Schlottermüller M., Himmel N., Schledjewski R. Effects of tape tension on residual stress in thermoplastic composite filament winding. Journal of Thermoplastic Composite Materials, 2005, vol. 18, no. 6, pp. 469–487. doi: 10.1177/0892705705054409
-
Obraztcov I.F., Bulychev L.A., Vasilev V.V. et.al. Structural Mechanics of Aircraft. Tutorial. Moscow, Mashinostroenie Publ., 1986, 536 p. (in Russian)
-
Thwaits J.J. The elastic deformation of a rod with helical anisotropy. International Journal of Mechanical Sciences, 1977, vol. 19, no. 3, pp. 161–168. doi: 10.1016/0020-7403(77)90075-3
-
Mostafa N.H., Ismarrubie Z.N., Sapuan S.M., Sultan M.T.H. Fibre prestressed composites: theoretical and numerical modelling of unidirectional and plain-weave fibre reinforcement forms. Composite Structures, 2017, vol. 159, pp. 410–423. doi: 10.1016/j.compstruct.2016.09.090
-
Hashimoto H. Intelligent winding machine of plastic films for preventing both wrinkles and slippages. Modern Mechanical Engineering, 2016, vol. 6, no. 1, pp. 20–31. doi: 10.4236/mme.2016.61003
-
Hashimoto H., Jeenkour P., Mongkolowongrojn M. Optimum winding tension and nip-load into wound webs for protecting wrinkles and slippage. Journal of Advanced Mechanical Design, Systems, and Manufacturing, 2010, vol. 4, no. 1, pp. 214–225. doi: 10.1299/jamdsm.4.214
-
Kutin A., Musalimov V. Winding density regulation in the composite shell manufacture. Proc. IEEE International Conference on Mechatronics (ICM 2019), 2019, pp. 332–336. doi: 10.1109/ICMECH.2019.8722860
-
Kutin A.Yu., Musalimov V.M., Polyakov A.S. Designing composite winding and managing the process of its formation. Journal of Instrument Engineering, 2018, vol. 61, no. 2, pp. 160–166. (in Russian). doi: 10.17586/0021-3454-2018-61-2-160-166
-
Kut'in A.Yu. Assessing the error when determining a length of textile material. Izvestiya Vysshikh Uchebnykh Zavedenii, Seriya Teknologiya Tekstil'noi Promyshlennosti, 2004, no. 2, pp. 117–118. (in Russian)
-
Komkov M., Tarasov V., Borodulin A. Spiral winding of ends of composite shells with cylindrical and conical shapes. Herald of the Bauman Moscow State Technical University. Series Mechanical Engineering, 2012, no. 4, pp. 78–85. (in Russian)
-
Mutasher S., Mir-Nasari N., Lin L.C. Small-scale filament winding machine for producing fiber composite products. Journal of Engineering Science and Technology, 2012, vol. 7, no. 2, pp. 156–168.
-
Zhong W., Yang H., Li H., Xu J. Control system design of robotized filament winding for elbow pipe. Proc. 2nd International Conference on Measurement, Information and Control (ICMIC 2013), 2013, vol. 2, pp. 1081–1085. doi: 10.1109/MIC.2013.6758147
-
Quanjin M., Rejab M.R.M., Idris M.S., Kumar N.M., Merzuki M.N.M. Robotic filament winding technique (RFWT) in industrial application: A review of state of the art and future perspectives. International Research Journal of Engineering and Technology, 2018, vol. 5, no. 12, pp. 1668–1675.
-
Sorrentino L., Marchetti M., Bellini C., Delfini A., Del Sette F. Manufacture of high performance isogrid structure by robotic filament winding. Composite Structures, 2017, vol. 164, pp. 43–50. doi: 10.1016/j.compstruct.2016.12.061
-
Musalimov V., Aryassov G., Zhigailov S., Rõbak D., Penkov I. Motion imitation of the human pelvic and hip joints. AIP Conference Proceedings, 2018, vol. 2029, pp. 020046. doi: 10.1063/1.5066508
-
Zhigailov S., Musalimov V., Aryassov G., Penkov I. Modelling and simulation of human lower–limb motion. International Review on Modelling and Simulations, 2016,vol. 9, no. 2, pp. 114–123. doi: 10.15866/iremos.v9i2.8358