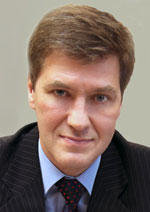
Nikiforov
Vladimir O.
D.Sc., Prof.
doi: 10.17586/2226-1494-2021-21-2-275-282
A one-step optimization method for a compressor wheel of a microturbine engine
Read the full article

For citation:
Bulat M.P., Chernyshov M.V., Vokin L.O., Kurnukhin A.A. A one-step optimization method for a compressor wheel of a microturbine engine. Scientific and Technical Journal of Information Technologies, Mechanics and Optics, 2021, vol. 21, no. 2, pp. 275–282 (in Russian). doi: 10.17586/2226-1494-2021-21-2-275-282
Abstract
The work deals with the design acceleration of optimal turbomachines. For its solution, it is proposed to apply mathematical optimization methods at the initial design stage. The goal of the study was to develop a one-step algorithm for optimal compressor wheel design. The application of the algorithm has a decisive advantage in comparison to the traditional iterative method for turbomachines design. The task of designing a turbomachine is multi-parameter and interdisciplinary and involves different requirements, which often contradict each other, consequently several optimality criteria can be used simultaneously. The traditional method consists in performing one-dimensional thermal and gas-dynamic calculations with subsequent refinement using numerical study. Further fine-tuning of the wheel geometry includes variation of the blade angle at the exit from the impeller, as well as of the height of the flow path at the exit from the wheel. One-step global optimization was performed by using a particle swarm algorithm involving eleven variable parameters. The objective function is thermodynamic efficiency, calculated by stagnation parameters. The authors compare the results of calculating the geometry of the centrifugal compressor wheel by the traditional sequential method and by the newly developed global optimization method. The compressor wheel has an outer diameter of 200 mm, the diameter of the hub is 52 mm, the rotational speed is 60,000 rpm and the required compression ratio is 3.7. In the traditional optimization method, the blade angles and the profile thickness are varied in three or four blade cross sections. The novelty of the developed one-step algorithm consists in the optimization of the initially three-dimensional shape of the flow path. Testing has shown that the one-step global optimization method provides an efficiency gain of about 2 %. Compared to the traditional method, the required time decreased 6 to 18 times. The proposed method can be applied to the design of turbomachines of various dimensions. The developed algorithm can be used as a basis for external modules in various existing packages, such as Ansys, Comsol and SolidWorks.
Acknowledgements. This work was financially supported by the Ministry of Science and Higher Education of Russian Federation during the implementation of the project “Creating a leading scientific and technical reserve in the development of advanced technologies for small gas turbine, rocket and combined engines of ultra-light launch vehicles, small spacecraft and unmanned aerial vehicles that provide priority positions for Russian companies in emerging global markets of the future”, No. FZWF-2020-0015.
References
- Li Z., Zheng X. Review of design optimization methods for turbomachinery aerodynamics. Progress in Aerospace Sciences, 2017, vol. 93, pp. 1–23. doi: 10.1016/j.paerosci.2017.05.003
- Zhang J.-Y., Cai S.-J., Li Y.-J., Zhou X., Zhang Y.-X. Optimization design of multiphase pump impeller based on combined genetic algorithm and boundary vortex flux diagnosis. Journal of Hydrodynamics, 2017, vol. 29, no. 6, pp. 1023–1034. doi: 10.1016/S1001-6058(16)60816-8
- Benturki M., Dizene R., Ghenaiet A. Multi-objective optimization of two-stage centrifugal pump using NSGA-II algorithm. Journal of Applied Fluid Mechanics, 2018, vol. 11, no. 4, pp. 929–943. doi: 10.29252/jafm.11.04.28509
- Zhang Y., Xu S., Wan Y. Performance improvement of centrifugal compressors for fuel cell vehicles using the aerodynamic optimization and data mining methods. International Journal of Hydrogen Energy, 2020, vol. 45, no. 19, pp. 11276–11286. doi: 10.1016/j.ijhydene.2020.02.026
- Ma S.-B., Afzal A., Kim K.-Y. Optimization of ring cavity in a centrifugal compressor based on comparative analysis of optimization algorithms. Applied Thermal Engineering, 2018, vol. 138, pp. 633–647. doi: 10.1016/j.applthermaleng.2018.04.094
- Lapshin K.L. Optimization of flow paths of multistage turbines. St. Petersburg, St. Petersburg University Publ., 1992, 196 p. (in Russian)
- Tahan M., Tamiru A.L., Muhammad M. Design optimization of industrial gas turbines using simulated annealing algorithms. MATEC Web of Conferences, 2018, vol. 225, pp. 02018. doi: 10.1051/matecconf/201822502018
- Samora I., Franca M.J., Schleiss A.J., Ramos H.M. Simulated annealing in optimization of energy production in a water supply network. Water Resources Management, 2016, vol. 30, no. 4, pp. 1533–1547. doi: 10.1007/s11269-016-1238-5
- Khachaturyan A., Semenovsovskaya S., Vainshtein B. The thermodynamic approach to the structure analysis of crystals. Acta Crystallographica Section A: Foundations of Crystallography, 1981, vol. 37, no. 5, pp. 742–754. doi: 10.1107/S0567739481001630
- Shen X., Yang H., Chen J., Zhu X., Du Z. Aerodynamic shape optimization of non-straight small wind turbine blades. Energy Conversion and Management, 2016, vol. 119, pp. 266–278. doi: 10.1016/j.enconman.2016.04.008
- Shim H.-S., Afzal A., Kim K.-Y., Jeong H.-S. Three-objective optimization of a centrifugal pump with double volute to minimize radial thrust at off-design conditions. Proceedings of the Institution of Mechanical Engineers, Part A: Journal of Power and Energy, 2016, vol. 230, no. 6, pp. 598–615. doi: 10.1177/0957650916656544
- Yang X.-S. Engineering Optimization: An Introduction with Metaheuristic Applications. John Wiley & Sons, 2010, 347 p.
- Lu X.Y., Lu Z.Q. Numerical optimization for radiated noises of centrifugal pumps in the near-field and far-field based on a novel MLGA-PSO algorithm. Journal of Vibroengineering, 2017, vol. 19, no. 7, pp. 5589–5605. doi: 10.21595/jve.2017.18717
- Derakhshan S., Mohammadi B., Nourbakhsh A. Efficiency improvement of centrifugal reverse pumps. Journal of Fluids Engineering, Transactions of the ASME, 2009, vol. 131, no. 2, pp. 0211031–0211039. doi: 10.1115/1.3059700
- Kang H.-S., Kim Y.-J. A study on the multi-objective optimization of impeller for high-power centrifugal compressor. International Journal of Fluid Machinery and Systems, 2016, vol. 9, no. 2, pp. 143–149. doi: 10.5293/IJFMS.2016.9.2.143
- Wang L., Kolios A., Nishino T., Delafin P.-L., Bird T. Structural optimisation of vertical-axis wind turbine composite blades based on finite element analysis and genetic algorithm. Composite Structures, 2016, vol. 153, pp. 123–138. doi: 10.1016/j.compstruct.2016.06.003
- Tao R., Xiao R., Zhu D., Wang F. Multi-objective optimization of double suction centrifugal pump. Proceedings of the Institution of Mechanical Engineers, Part C: Journal of Mechanical Engineering Science, 2018, vol. 232, no. 6, pp. 1108–1117. doi: 10.1177/0954406217699020
- Wang Y., Huo X. Multiobjective optimization design and performance prediction of centrifugal pump based on orthogonal test. Advances in Materials Science and Engineering, 2018, vol. 2018, pp. 6218178. doi: 10.1155/2018/6218178
- Shim H.-S., Kim K.-Y., Choi Y.-S. Three-objective optimization of a centrifugal pump to reduce flow recirculation and cavitation. Journal of Fluids Engineering, Transactions of the ASME, 2018, vol. 140, no. 9, pp. 091202. doi: 10.1115/1.4039511
- Wang K., Luo G., Li Y., Xia R., Liu H. Multi-condition optimization and experimental verification of impeller for a marine centrifugal pump. International Journal of Naval Architecture and Ocean Engineering, 2020, vol. 12, pp. 71–84. doi: 10.1016/j.ijnaoe.2019.07.002
- Seleznev K.P., Galerkin Iu.B., Anisimov S.A., Mitrofanov V.P., Podobuev Iu.S. Theory and design of turbocompressors. Leningrad, Mashinostroenie Publ., 1985, 392 p. (in Russian)
- Neverov V.V., Kozhukhov Y.V., Yablokov A.M., Lebedev A.A. Optimization of a centrifugal compressor impeller using CFD: The choice of simulation model parameters. IOP Conference Series: Materials Science and Engineering, 2017, vol. 232, no. 1, pp. 012037. doi: 10.1088/1757-899X/232/1/012037
- Bulat M.P., Bulat P.V. The analysis centric isentropic compression waves. World Applied Sciences Journal, 2013, vol. 27, no. 8, pp. 1023–1026. doi: 10.5829/idosi.wasj.2013.27.08.13719