Menu
Publications
2025
2024
2023
2022
2021
2020
2019
2018
2017
2016
2015
2014
2013
2012
2011
2010
2009
2008
2007
2006
2005
2004
2003
2002
2001
Editor-in-Chief
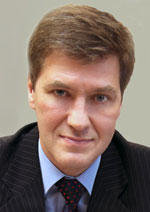
Nikiforov
Vladimir O.
D.Sc., Prof.
Partners
doi: 10.17586/2226-1494-2021-21-3-386-393
The investigation of dynamic properties of 3D-printed steel parts
Read the full article

Article in Russian
For citation:
Abstract
For citation:
Eliseev D.P., Konakov R.D. The investigation of dynamic properties of 3D-printed steel parts.Scientific and Technical Journal of Information Technologies, Mechanics and Optics, 2021, vol. 21, no. 3, pp. 386–393 (in Russian).
doi: 10.17586/2226-1494-2021-21-3-386-393
Abstract
Additive technologies are promising for manufacturing parts of metal navigation devices with complex shapes. Finite element analysis is used during the designing of such items. The modeling accuracy is determined by the correctness of the specified physical properties of materials. The properties of materials used in 3D printing significantly differ from the ones used in the traditional manufacturing. Researchers focus on such characteristics as Young’s modulus, Poisson’s ratio, hardness and strength. Meanwhile, some applications require dynamic properties. The paper presents the investigation and comparison of damping properties of three steel parts produced by different methods. The first part is manufactured by 3D printing with melting in the transverse direction, and the second part is done by melting in the longitudinal direction, while the third one is traditionally manufactured. The parts are shaft shaped with constant cross-section and have the same geometric dimensions. The TIRA TV 5220 / LS-120 stand is used. A piezoelectric accelerometer is installed at the loose end of the part. The tests are carried out in the frequency range from 15 to 3500 Hz and with an acceleration of 19.6 m/s2 (2 g). The accelerometer output is used to calculate the damping coefficient. The results are verified by comparison with the finite element modeling results. The damping coefficients of transverse and longitudinal 3D-printed parts are 0.022 and 0.006, respectively. The damping coefficient of the traditional manufactured part is 0.023. The difference of 3D-printed parts damping coefficients can be explained by the denser fusion of powder granules when printing one layer than between layers. In this case, a crystal structure with greater rigidity in the printing plane is formed and it limits the dissipation of vibration energy due to internal friction. Finite element modeling shows mismatch between the experimental and calculated values of the printed parts natural frequencies. Considering that the values of natural frequencies are largely determined by Young’s modulus, a parametric optimization of its value is carried out. It was found that the value of Young’s modulus does not correspond to the values determined during tensile tests for similar samples. Thus, 3D-printed parts have different vibration and static stiffness. This is not typical for metals and should be taken into account in simulations. The research results can be used in the simulation model development of steel 3D-printed parts and in the design of digital twins for navigation devices. It allows one to estimate vibration resistance of promising products at the early stages of their design and to optimize the construction minimizing stress.
Keywords: additive technologies, vibration exposure, finite element modeling, damping coefficient, simulation, digital twin, vibration stiffness
References
References
1. Iulmetova O.S., Shcherbak A.G., Chelpanov I.B. Special Manufacturing Techniques for Precision Units and Elements of gyroscopic Devices. Tutorial. St. Petersburg, ITMO University, 2017, 131 p. (in Russian)
2. Chekhovich A. 5 characteristics of metal powders for 3D printing. Available at: https://blog.iqb.ru/metals-for-3d-printing (accessed: 23.04.2021). (in Russian)
3. Tit M.A., Epifanov D.O., Belyaev Ya.V. The experience of additive technology application in design and manufacturing devices of CSRI «Electropribor». Proc. 22st Conference of Young Scientists "Navigation and Motion Control" (with international participants), St. Petersburg, Concern CSRI Elektropribor, 2020, pp. 69–71. (in Russian)
4. Eliseev D.P., Malashenkov K.S. Quality and mechanical properties of austenitic steel samples fabricated by an additive technology. Russian Metallurgy (Metally), 2020, vol. 2020, no. 11, pp. 1308–1313. doi: 10.1134/S0036029520110063
5. Valetov V.A. Additive Technologies (State and Prospects). Tutorial. St. Petersburg, ITMO University, 2015, 58 p. (in Russian)
6. Zlenko M.A., Popovich A.A., Mutylina I.N. Additive Technologies in Mechanical Engineering. St. Petersburg, SPbPU Publ., 2013, 222 p. (in Russian).
7. Peshekhonov V.G. The author of precision gyroscope. Gyroscopy and Navigation, 2020, vol. 11, no. 2, pp. 188–192. doi: 10.1134/S2075108720020042
8. Bezmen G.V., Shevchenko A.N., Kostin P.N., Berzeitis A.N., Bezmen V.S., Petrov V.I. A Two-frequency spin oscillation system for a quantum angular rate sensor. Gyroscopy and Navigation, 2020, vol. 11, no. 2, pp. 115–123. doi: 10.1134/S2075108720020030
9. Evstifeev M.I., Eliseev D.P. Teaching method of gyroscopic devices design basics. Modern technologies in control, automation and information processing: Proc. of the 26th International Scientific and Technical Conference, Moscow, 2017, pp. 120–121. (in Russian)
10. Glukhov V.V., Turichin G.A. Economic efficiency of technology of direct laser growing in the industry. Theoretical Foundations of Industrial Policy Formation. St. Petersburg, SPbPU Publ., 2015, pp. 176–190. (in Russian)
11. Peshekhonov V.G. The outlook for gyroscopy. Gyroscopy and Navigation, 2020, vol. 11, no. 3, pp. 193–197. doi: 10.1134/S2075108720030062
12. Lewandowski J.J., Seifi M. Metal additive manufacturing: A review of mechanical properties. Annual Review of Materials Research, 2016, vol. 46, pp. 151–186. doi: 10.1146/annurev-matsci-070115-032024
13. Bershtam Ia.N., Evstifeev M.I., Eliseev D.P. Studying the alloys with high internal damping in the structure of MEMS gyro. Proc. of the 29th Conference in Memory of N.N. Ostryakov, 2014, pp. 65–72. (in Russian)