Menu
Publications
2025
2024
2023
2022
2021
2020
2019
2018
2017
2016
2015
2014
2013
2012
2011
2010
2009
2008
2007
2006
2005
2004
2003
2002
2001
Editor-in-Chief
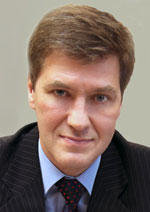
Nikiforov
Vladimir O.
D.Sc., Prof.
Partners
doi: 10.17586/2226-1494-2022-22-2-339-347
Model of the acoustic path of a separatecombined optical-acoustic transducer
Read the full article

Article in Russian
For citation:
Abstract
For citation:
Fedorov A.V., Bychenok V.A., Berkutov I.V., Alifanova I.E. Model of the acoustic path of a separate-combined optical-acoustic transducer. Scientific and Technical Journal of Information Technologies, Mechanics and Optics, 2022, vol. 22, no. 2, pp. 339–347 (in Russian). doi: 10.17586/2226-1494-2022-22-2-339-347
Abstract
Ultrasonic testing methods occupy one of the key positions in flaw detection, structurescopy, in assessing the strength characteristics of materials and the stress-strain state of products. The method is based on the phenomenon of acoustoelasticity and makes it possible to control the stress-strain state of products by changing the propagation velocity of a longitudinal subsurface ultrasonic wave. To excite acoustic waves, a separate-combined optical-acoustic transducer and a laser-ultrasonic flaw detector are used. The design of a separate-combined optical-acoustic transducer should ensure the measurements accuracy of the time it takes for a longitudinal subsurface wave to reach the receiver of acoustic oscillations. To analyze the recorded acoustic signals and extract from them the signal of a longitudinal subsurface wave, in this work, a finite element model of the acoustic path of a dual-coupled optical-acoustic transducer is proposed and developed. The finite element model was implemented in the COMSOL Multiphysics software package using an explicit solver based on the discontinuous Galerkin method. The developed finite element model makes it possible to visualize the displacement fields of acoustic oscillations, obtain A-scans, and calculate the time of arrival of a longitudinal subsurface wave at the receiver of the optical-acoustic transducer. The calculated values of the arrival time of a longitudinal subsurface wave at the receiver of an optical-acoustic transducer are compared with the results of a full-scale experiment. Calculations and full-scale experiments were performed for steel plates of various thicknesses. The adequacy of the model was confirmed using the Fisher criterion (F-measure). The A-scans obtained as a result of the simulation made it possible to identify the signals recorded by the optical-acoustic transducer: the signal of the longitudinal subsurface wave, the signals of the head and reflected transverse waves, and the intrinsic noise of the optoacoustic transducer. The developed model makes it possible to single out the signal of the longitudinal subsurface wave among the recorded signals of the optical-acoustic transducer. The proposed model can be used in the design of new optical-acoustic transducers, as well as in non-destructive testing (NDT) and materials science.
Keywords: residual stresses, acoustic method, non-destructive testing, longitudinal subsurface wave, computer simulation
References
References
-
Kretov E.F. Ultrasonic Flaw Detection in Power Engineering. St. Petersburg, SVEN Publ., 2014, 312 p. (in Russian)
-
Kliuev V.V. Non-Destructive Testing. V.3. Ultrasonic Examination. Moscow, Mashinostroenie Publ., 2004, 864 p. (in Russian)
-
Karabutov A.A., Nguen Xuan Man, Pham Manh Hao, Cherepetskaya E.B., Shibaev I.A. The possibility of controlling the structure and properties of fiber-reinforced concrete method of laser-ultrasonic structuroscopy.Mining Informational and Analytical Bulletin, 2016, no. 7, pp. 32–41. (in Russian)
-
Stepanova K.A., Kinzhagulov I.Y., Yakovlev Y.O., Kovalevich A.S., Ashikhin D.S., Alifanova I.E. Applying laser-ultrasonic and acoustic-emission methods to nondestructive testing at different stages of deformation formation in friction stir welding. Russian Journal of Nondestructive Testing, 2020, vol. 56, no. 3, pp. 191–200. https://doi.org/10.1134/S1061830920030122
-
Marusina M.Y., Fedorov A.V., Bychenok V.A., Berkutov I.V. Evaluation of the influence of external factors in ultrasonic testing of stress-strain states. Measurement Techniques, 2017, vol. 59, no. 11, pp. 1165–1169. https://doi.org/10.1007/s11018-017-1109-3
-
Marusina M.Y., Fedorov A.V., Prokhorovich V.E., Berkutov I.V., Bychenok V.A., Tkacheva N.V., Mayorov A.L. Development of acoustic methods of control of the stress-strain state of threaded connection. Measurement Techniques, 2018, vol. 61, no. 3, pp. 297–302. https://doi.org/10.1007/s11018-018-1424-3
-
Nikitina N.E. Аcoustoelasticity. Practical Experience. Nizhny Novgorod, TALAM Publ., 2005, 208 p. (in Russian)
-
Fedorov A.V., Bychenok V.A., Berkutov I.V., Alifanova I.E., Khoshev A.E. Methodology for assessing the uncertainty of measurements of mechanical stresses by the ultrasonic method with the help of an optical-acoustic separate-combined transducer. Journal of Physics: Conference Series, 2021, vol. 2127, no. 1, pp. 012036. https://doi.org/10.1088/1742-6596/2127/1/012036
-
Fedorov A.V., Bychenok V.A., Berkutov I.V., Alifanova I.E. Methodology for evaluation the uncertainty of measurement of mechanical stress by the ultrasonic method with the help of an optical-acoustic separate-combined transducer. Testing. Diagnostics, 2021, vol. 24, no. 7(277), pp. 56–61. (in Russian). https://doi.org/10.14489/td.2021.07.pp.056-061
-
Karabutov A.A. Laser ultrasonic flaw detector. Patent RU2381496C1. 2010. (in Russian)
-
Razygraev N.P. Physics, terminology and technology in ultrasonic testing with head waves. Defektoskopija, 2020, no. 9, pp. 3–19. (in Russian). https://doi.org/10.31857/S0130308220090018
-
Baev A.R., Mayorov A.L., Asadchaya M.V., Levkovich N.V. Zhavoronkov K.G. Features of the surface and subsurface waves application for ultrasonic evaluation of physicomechanical properties of solids. Part 1. Influence of the geometrical parameters. Devices and Methods of Measurements, 2018, vol. 9, no. 4, pp. 325–336. (in Russian). https://doi.org/10.21122/2220-9506-2018-9-4-325-336
-
Petrov K.V. Shadow-mirror technique for testing cylindrical products using electromagnetic acoustic transducers. Dissertation for the degree of candidate of technical sciences. Izhevsk, Kalashnikov Izhevsk State Technical University, 2020. Available at: https://etu.ru/assets/files/nauka/dissertacii/2020/petrov/petrov-k.v.-dissertaciya.pdf (accessed: 19.01.2022). (inRussian)
-
Tapkov K.A. Scientific substantiation of the methodology for estimating the residual stresses in differentially hardened rails based on the acoustoelasticity phenomenon and mathematical simulation. Dissertation for the degree of candidate of technical sciences. Izhevsk, Kalashnikov Izhevsk State Technical University, 2020. Available at: http://udman.ru/ru/scientific-activity/dissertation-council/protection/dissertatsiya-tapkova-kirilla-aleksandrovicha/Тапков%20К.А.%20-%20Диссертация.pdf (accessed: 19.01.2022). (in Russian)
-
Berkutov I.V. Research and development of the acoustic tensometry method for special threaded connections. Dissertation for the degree of candidate of technical sciences. ITMO University, 2018. Available at: https://search.rsl.ru/ru/record/01009876980 (accessed: 19.01.2022). (in Russian)
-
Ermolov I.N. Theory and Practice of Ultrasonic Testing. Moscow, Mashinostroenie Publ., 1981, 240 p. (in Russian)
-
Iankin S. DG-FEM: new technology for large scale calculations of acoustic and elastic wave propagation in COMSOL Multiphysics®. Available at: https://www.comsol.ru/video/dg-fem-new-technology-for-acoustic-and-elastic-wave-modeling-on-large-scales-in-comsol-webinar-ru (accessed: 19.01.2022). (in Russian)
-
Tikhonov A.N., Samarskii A.A. Equations of Mathematical Physics. Moscow, Nauka Publ., 1977, 736 p. (in Russian)
-
Torshina I.P., Yakushenkov Y.G. Valuation of adequacy for computer model of opto-electronic system. Journal of Instrument Engineering, 2009, vol. 52, no. 9, pp. 63–67. (in Russian)
-
Orlov V.Iu., Volkov E.M. Basics of the Statistical Processing of Scientific Experiment Results. Yaroslavl, Yaroslavl State University Publ., 2014, 68 p. (in Russian)