Menu
Publications
2025
2024
2023
2022
2021
2020
2019
2018
2017
2016
2015
2014
2013
2012
2011
2010
2009
2008
2007
2006
2005
2004
2003
2002
2001
Editor-in-Chief
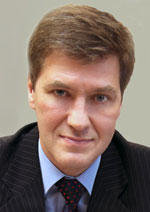
Nikiforov
Vladimir O.
D.Sc., Prof.
Partners
doi: 10.17586/2226-1494-2023-23-4-803-811
Modeling of the process of spherical form correction for rotors of electrostatically suspended gyros
Read the full article

Article in Russian
For citation:
Abstract
For citation:
Tit M.A., Belyaev S.N., Shcherbak A.G., Yulmetova O.S. Modeling of the process of spherical form correction for rotors of electrostatically suspended gyros. Scientific and Technical Journal of Information Technologies, Mechanics and Optics, 2023, vol. 23, no. 4, pp. 803–811 (in Russian). doi: 10.17586/2226-1494-2023-23-4-803-811
Abstract
Improvement of the manufacturing technology for gyroscopic devices, which autonomously generate motion parameters of moving objects, has strategic importance and priority for various industries. The object of current research is a spherical rotor of an electrostatically suspended gyroscope which geometric parameters determine the accuracy characteristics of the device. The paper presents results of the process modeling of spherical form correction for rotors of electrostatically suspended gyroscopes at the stage of its manufacture during the coating deposition process. The proposed mathematical model of the deposition process is based on the placement of a movable screen with a hole between a rotor and a spray source. The axis of the hole lies on the dynamic axis of the rotor and it provides a formation of a spherical segment on the coating rotor surface. During deposition of an additional layer, the screen or rotor moves along the dynamic axis of the rotor changing the distance between the rotor and the screen, and there is additional rotation of the rotor around its dynamic axis. It allows adjusting the curvature of the formed coating on the rotor surface. An analytical model of the technological process for correcting the shape of spherical rotors of electrostatically suspended gyroscopes has been developed. A mathematical description, control factors and significant parameters of the process are given. The results of practical testing of the developed model are presented. The presented mathematical model makes it possible to correct the shape of the rotors during the deposition of a functional coating expanding the technological possibilities and increasing the accuracy of rotors.
Keywords: coating, shape correction, deposition, modeling, spherical rotor
References
References
- Peshekhonov V.G. The outlook for gyroscopy. Gyroscopy and Navigation, 2020, vol. 11, no. 3, pp. 193–197. https://doi.org/10.1134/S2075108720030062
- Gusinsky V.Z., Litmanovich Y.A., Lesyuchevsky V.M. Spacecraft attitude determination using electrostatically suspended gyros. IFAC Proceedings Volumes, 2001, vol. 34, no. 15, pp. 26–31. https://doi.org/10.1016/S1474-6670(17)40700-2
- Landau B.E., Belash A.A., Gurevich S.S., Levin S.L., Romanenko S.G., Tsvetkov V.N. Electrostatic gyroscope in spacecraft attitude reference systems. Gyroscopy and Navigation, 2021, vol. 12, no. 3, pp. 247–253. https://doi.org/10.1134/s2075108721030056
- Iulmetova O.S. Ion-plasma and laser technologies in gyroscopic instrumentation. Thesis for the degree of Doctor of Technical Sciences. St. Petersburg, Concern CSRI Elektropribor, 2018, 244 p. (in Russian)
- Grigoriev S., Vereschaka A., Zelenkov V., Sitnikov N., Bublikov J., Milovich F., Andreev N., Sotova C. Investigation of the influence of the features of the deposition process on the structural features of microparticles in PVD coatings. Vacuum, 2022, vol. 202, pp. 111144. https://doi.org/10.1016/j.vacuum.2022.111144
- Maksakova O., Simoẽs S., Pogrebnjak A., Bondar O., Kravchenko Y., Beresnev V., Erdybaeva N. The influence of deposition conditions and bilayer thickness on physical-mechanical properties of CA-PVD multilayer ZrN/CrN coatings. Materials Characterization, 2018, vol. 140, pp. 189–196. https://doi.org/10.1016/j.matchar.2018.03.048
- Fomichev A.M., Shcherbak A.G., Jul'metova O.S., Beljaev S.N. Device for spattering of thin film coatings on spherical rotor of electrostatic gyroscope. Patent RU2555699C1, 2015. (in Russian)
- Ou Y.X., Wang H.Q., Ouyang X., Zhao Y.Y., Zhou Q., Luo C.W., Hua Q.S., Ouyang X.P., Zhang S. Recent advances and strategies for high-performance coatings. Progress in Materials Science, 2023, vol. 136, pp. 101125. https://doi.org/10.1016/j.pmatsci.2023.101125
- Makhaev E.A., Ryabova L.P., Chesnokov P.A., Shcherbak A.G., Kuznetcov S.A., Martiushov G.G. Development of a construction and manufacturing technology for the cryogyroscope rotor. Proc. of the 30th Conference of Memory N.N. Ostryakov. St. Petersburg, 2016, pp. 116–123. (in Russian)
- Dubrovskiy A.R., Okunev M., Makarova O., Kuznetsov S. Corrosion resistance of the substrates for the cryogenic gyroscope and electrodeposition of the superconductive niobium coatings. Journal of Physics: Conference Series, 2017, vol. 857, no. 1, pp. 012008. https://doi.org/10.1088/1742-6596/857/1/012008
- Tit M.A., Yulmetova O.S., Sisyukov A.N. Analysis of niobium thin film modification based on thermodynamic approach. Proc. of the 2020 IEEE Conference of Russian Young Researchers in Electrical and Electronic Engineering (EIConRus), 2020, pp. 1049–1052. https://doi.org/10.1109/eiconrus49466.2020.9038932
- Tit M.A., Belyaev S.N. Effect of Stoichiometric Composition on the Functional Characteristics of Thin-Film Surface Structures on Gyroscope Components. Inorganic Materials: Applied Research, 2020, vol. 11, no. 6, pp. 1370–1377. https://doi.org/10.1134/s2075113320060283
- Tit M.A., Yulmetova O.S., Andreeva V.D., Sisyukov A.N., Yulmetova R.F. Application of niobium nitride thin films for improvement of performance characteristics of cryogenic gyroscope. Proc.of the 2021 IEEE Conference of Russian Young Researchers in Electrical and Electronic Engineering (ElConRus), 2021, pp. 1232–1235. https://doi.org/10.1109/ElConRus51938.2021.9396714
- Scherbak A.G., Yulmetova O.S., Contrast image formation based on thermodynamic approach and surface laser oxidation process for optoelectronic read-out system. Optics & Laser Technology, 2018, vol. 101, pp. 242–247. https://doi.org/10.1016/j.optlastec.2017.11.030
- Yulmetova O.S., Scherbak A.G. Composition analysis of thin films formed on beryllium surfaces under pulsed laser action by the method of chemical thermodynamics. International Journal of Advanced Manufacturing Technology, 2018, vol. 97, no. 9-12, pp. 3231–3236. https://doi.org/10.1007/s00170-018-2216-2
- Yulmetova O.S., Tumanova M.A. Laser marking of contrast images for optical read-out systems. Journal of Physics: Conference Series, 2017, vol. 917, no. 5, pp. 052007. https://doi.org/10.1088/1742-6596/917/5/052007
- Yulmetova O.S., Tit M.A., Sisyukov A.N., Yulmetova R.F. Comparative analysis of electrochemical and laser marking for gyroscopic application. Proc. of the 2020 IEEE Conference of Russian Young Researchers in Electrical and Electronic Engineering (EIConRus), 2020, pp. 1053–1055. https://doi.org/10.1109/EIConRus49466.2020.9039076
- Chen L., Zhao Y., Song B., Yu T., Liu Z. Modeling and simulation of 3D geometry prediction and dynamic solidification behavior of Fe-based coatings by laser cladding. Optics & Laser Technology, 2021, vol. 139, pp. 107009. https://doi.org/10.1016/j.optlastec.2021.107009
- Katranidis V., Gu S., Allcock B., Kamnis S. Experimental study of high velocity oxy-fuel sprayed WC-17Co coatings applied on complex geometries. Part A: Influence of kinematic spray parameters on thickness, porosity, residual stresses and microhardness. Surface and Coatings Technology, 2017, vol. 311, pp. 206–215. https://doi.org/10.1016/j.surfcoat.2017.01.015
- Sahoo D.K., Neupane N., Chaudhary S. Predicting the coating geometries of friction surfaced aluminium cladding over carbon steel by artificial neural network modeling. Materials Today: Proceedings, 2023, in press. https://doi.org/10.1016/j.matpr.2023.01.056
- Paturi U.M.R., Cheruku S., Geereddy S.R. Process modeling and parameter optimization of surface coatings using artificial neural networks (ANNs): State-of-the-art review. Materials Today: Proceedings, 2021, vol. 38, part 5, pp. 2764–2774. https://doi.org/10.1016/j.matpr.2020.08.695
- Tit M.A., Landau B.E., Filippov A.Y., Shcherbak A.G. Ball gyroscope rotor manufacturing method. Patent RU2743492C1, 2020. (in Russian)