Menu
Publications
2025
2024
2023
2022
2021
2020
2019
2018
2017
2016
2015
2014
2013
2012
2011
2010
2009
2008
2007
2006
2005
2004
2003
2002
2001
Editor-in-Chief
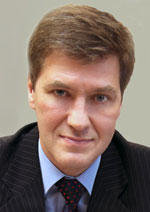
Nikiforov
Vladimir O.
D.Sc., Prof.
Partners
doi: 10.17586/2226-1494-2023-23-5-1056-1064
Analytical and simulation modeling of flexible joints for mechatronic and robotic systems
Read the full article

Article in Russian
For citation:
Abstract
For citation:
Rakshin E.A., Borisov I.I. Analytical and simulation modeling of flexible joints for mechatronic and robotic systems. Scientific and Technical Journal of Information Technologies, Mechanics and Optics, 2023, vol. 23, no. 5, pp. 1056–1064 (in Russian). doi: 10.17586/2226-1494-2023-23-5-1056-1064
Abstract
To operate in unstructured environments, robots must have the property of passivity which can be realized either through control algorithms or physical elastic elements. Flexible elements can be used to recover energy, absorb peak shock loads, and simplify the control system, generally reducing the requirements for accurate information about the robot’s environment. The modeling of flexible bodies, for example using the finite element method, is computationally demanding, which limits the simulation of the dynamic behavior of robots with flexible elements. In this paper, we propose an approach for analytical and simulation modeling of flexible joints using the planar case of a spatial spring model, which provides high speed simulation without loss of accuracy. The synthesis of the flexible joint model consists of numerical optimization of the nonlinear stiffness diagrams of the rotational and translational degrees of freedom for the planar case of the spatial spring model. The synthesized flexible joint model allows describing the relative motion of two links. In the first step of the synthesis, the flexible joint is optimized by finite element method to find the reference data of applied load and corresponding deformations. In the second stage, an optimization problem is solved to find nonlinear stiffness diagrams for the planar case of the spatial spring model; the criterion is to minimize the error between the reference data and the optimized spring model. In the third stage, the obtained results are verified by simulation and/or physical experiment. The method of analytical and simulation modeling of flexible joints with the help of spatial spring model is proposed, the procedure of optimization of stiffness of spring model is proposed, verification in simulation environment is carried out, full-scale experiment is carried out, comparison of simulations by finite element method, simulation with the help of spring model and results of full-scale experiment is provided. The proposed method allows the calculation of a simulation model of a flexible joint approximately twice as fast as the finite element method. The proposed model of flexible joint is necessary to increase the speed of simulation modeling of mechatronic and robotic systems with compliant hinges without loss of accuracy. Approbation of the method is planned for the design of locomotion, manipulation, wearable robots, and gripper devices.
Keywords: simulation modeling, flexible joints, elasticity theory, pseudo-rigid body model, optimization, surrogate model
Acknowledgements. is work is supported by the grant of the President of the Russian Federation (project No. MK-2081.2022.4).
References
Acknowledgements. is work is supported by the grant of the President of the Russian Federation (project No. MK-2081.2022.4).
References
- Peshkin M.A., Colgate J.E., Wannasuphoprasit W., Moore C.A., Gillespie R.B., Akella P. Cobot architecture. IEEE Transactions on Robotics and Automation, 2001, vol. 17, no. 4, pp. 377–390. https://doi.org/10.1109/70.954751
- Rezazadeh S., Abate A., Hatton R.L., Hurst J.W. Robot leg design: A constructive framework. IEEE Access, 2018, vol. 6, pp. 54369–54387. https://doi.org/10.1109/access.2018.2870291
- Hurst J.W., Rizzi A.A. Series compliance for an efficient running gait. IEEE Robotics & Automation Magazine, 2008, vol. 15, no. 3, pp. 42–51. https://doi.org/10.1109/mra.2008.927693
- Howell L.L. Compliant Mechanisms. New York, USA, Wiley, 2001, 459 p.
- Naves M. Design and optimization of large stroke flexure mechanisms. PhD Thesis. 2021. https://doi.org/10.3990/1.9789036549943
- Benscoter S.U. A theory of torsion bending for multi-cell beams. Journal of Applied Mechanics, 1954, vol. 21, no. 1, pp. 25–34. https://doi.org/10.1115/1.4010814
- Eltaher M.A., Alshorbagy A.E., Mahmoud F.F. Vibration analysis of Euler–Bernoulli nanobeams by using finite element method. Applied Mathematical Modelling, 2013, vol. 37, no. 7, pp. 4787–4797. https://doi.org/10.1016/j.apm.2012.10.016
- Ellenbroek M., Schilder J. On the use of absolute interface coordinates in the floating frame of reference formulation for flexible multibody dynamics. Multibody System Dynamics, 2018, vol. 43, no. 3, pp. 193–208. https://doi.org/10.1007/s11044-017-9606-3
- White D.R., Saigal S., Owen S.J. Meshing complexity: Predicting meshing difficulty for single part CAD models. Engineering with Computers, 2005, vol. 21, no. 1, pp. 76–90. https://doi.org/10.1007/s00366-005-0002-x
- Craig R.R., Jr. Coupling of substructures for dynamic analyses: An overview. Proc. of the 41st Structures, Structural Dynamics, and Materials Conference and Exhibit, 2000, pp. 1573. https://doi.org/10.2514/6.2000-1573
- Wiersma D.H., Boer S.E., Aarts R.G.K.M., Brouwer D.M. Design and performance optimization of large stroke spatial flexures. Journal of Computational and Nonlinear Dynamics, 2014, vol. 9, no. 1, pp. 011016. https://doi.org/10.1115/1.4025669
- Hopkins J.B., Culpepper M.L. Synthesis of multi-degree of freedom, parallel flexure system concepts via freedom and constraint topology (FACT) – Part I Principles. Precision Engineering, 2010, no. 34, no. 2, pp. 259–270. https://doi.org/10.1016/j.precisioneng.2009.06.008
- Yu Y-Q., Zhou P., Xu Q-P. Kinematic and dynamic analysis of compliant mechanisms considering both lateral and axial deformations of flexural beams. Proceedings of the Institution of Mechanical Engineers, Part C: Journal of Mechanical Engineering Science, 2019, vol. 233, no. 3, pp. 1007–1020. https://doi.org/10.1177/0954406218760956
- Yu Y-Q., Li Q., Xu Q-P. Pseudo-rigid-body dynamic modeling and analysis of compliant mechanisms. Institution of Mechanical Engineers, Part C: Journal of Mechanical Engineering Science, 2018, vol. 232, no. 9, pp. 1665–1678. https://doi.org/10.1177/0954406217707547
- Venkiteswaran V.K., Su H.J. A three-spring pseudorigid-body model for soft joints with significant elongation effects. Journal of Mechanisms and Robotics, 2016, vol. 8, no. 6, pp. 061001. https://doi.org/10.1115/1.4032862
- Hall A.R. The Pseudo-Rigid-Body Model for Fast, Accurate, Non-Linear Elasticity. A thesis submitted to the faculty of Brigham Young University in partial fulfillment of the requirements for the degree of Master of Science. 2013.
- Pei X., Yu J., Zong G., Bi S., Su H. The modeling of cartwheel flexural hinges. Mechanism and Machine Theory, 2009, no. 44, no. 10, pp. 1900–1909. https://doi.org/10.1016/j.mechmachtheory.2009.04.006
- Šalinić S., Nikolić A. A new pseudo-rigid-body model approach for modeling the quasi-static response of planar flexure-hinge mechanisms. Mechanism and Machine Theory, 2018, vol. 124, pp. 150–161. https://doi.org/10.1016/j.mechmachtheory.2018.02.011
- Stramigioli S. Modeling and IPC Control of Interactive Mechanical Systems: A Coordinate-Free Approach. Springer, 2001, XIII, 280 p. Lecture Notes in Control and Information Sciences; vol. 266. https://doi.org/10.1007/BFb0110400
- Folkertsma G.A. Energy-based and biomimetic robotics. PhD Thesis. 2017.
- Naves M., Brouwer D.M., Aarts R.G.K.M. Building block-based spatial topology synthesis method for large-stroke flexure hinges. Journal of Mechanisms and Robotics, 2017, vol. 9, no. 4, pp. 041006. https://doi.org/10.1115/1.4036223