Menu
Publications
2025
2024
2023
2022
2021
2020
2019
2018
2017
2016
2015
2014
2013
2012
2011
2010
2009
2008
2007
2006
2005
2004
2003
2002
2001
Editor-in-Chief
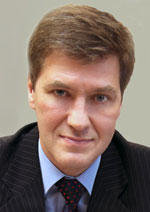
Nikiforov
Vladimir O.
D.Sc., Prof.
Partners
doi: 10.17586/2226-1494-2024-24-6-913-922
Investigation of the method of moving object weight measurement based onquasidistributed fiber Bragg gratings with temperature compensation
Read the full article

Article in Russian
For citation:
Abstract
For citation:
Moor I.D., Kozlova A.I., Korobkova U.R., Varzhel S.V., Kulikov A.V. Investigation of the method of moving object weight measurement based on quasi-distributed fiber Bragg gratings with temperature compensation. Scientific and Technical Journal of Information Technologies, Mechanics and Optics, 2024, vol. 24, no. 6, pp. 913–922 (in Russian). doi: 10.17586/2226-1494-2024-24-6-913-922
Abstract
Weight sensors are widely used in the freight transportation industry. In the systems for weighing vehicles while moving, ceramic, polymer, quartz piezoelectric sensors, load or hydraulic cells, strain gauges are used as sensitive elements. However, most electric sensors are susceptible to electromagnetic interference. Currently, fiber-optic sensors are most actively developed and put into operation due to their relatively low cost, small weight and size parameters, high measurement accuracy and complete passivity to electromagnetic disturbances. Fiber-optic sensors are most often implemented using fiber Bragg gratings, taking into account the convenience of their multiplexing. Mechanical deformations lead to a shift in the wavelength of the Bragg resonance of the grating. At the same time, the problem of using fiber gratings is associated with their sensitivity to temperature. To achieve high accuracy in measuring the deformation value, and accordingly, the weight characteristics of the object, it is necessary to eliminate or compensate for the effect of the sensor temperature on its readings. Most modern studies describe sensors that either operate in laboratory conditions or involve the use of an additional sensor that complicates the circuit for measuring temperature. The paper proposes a method for solving the problem of cross-sensitivity of a fiber diffraction structure to temperature and deformation. The method is based on the use of a pair of closely spaced gratings in the sensitive element of the sensor. One of the gratings has a constant period along the length, and the other has a variable one. The design of the sensitive element ensures the transfer of mechanical load only to the fiber grating with a constant period, and the temperature change equally affects both diffraction structures. A design solution for the sensitive element is proposed that allows for temperature effects compensation without using additional elements. A mathematical model of temperature effects is presented, allowing estimating the dependence of the temperature gradient on time for different thicknesses of the sensitive element. Modeling has showed that for a sample 0.95 cm thick, the temperature gradient inside the substrate is insignificant. With a sharp change in temperature, the equalization of the temperature field within the substrate at a level of 90 % occurs in no more than 2.5 s. The mechanical load on the sensitive element can pass relative to the fiber grating at different angles in connection with which the value of the shift of the central wavelength of the Bragg resonance was studied in detail depending on the point of application and direction of the load. The proposed technology may be of interest in the development and operation of automatic weight and size control systems with temperature compensation without the use of additional sensors. The proposed system is easy to operate and it has a low cost.
Keywords: temperature compensation, weight measurement method, fiber Bragg gratings, weight sensor, sensing element modeling, road damage, auto weight control
Acknowledgements. The research was carried out within the state assignment of the Ministry of Science and Higher Education of the Russian Federation (project No. FSER-2024-0006).
References
Acknowledgements. The research was carried out within the state assignment of the Ministry of Science and Higher Education of the Russian Federation (project No. FSER-2024-0006).
References
- Citir N., Gopisetti P., Ceylan H., Kim S. Evaluating the impact of overweight trucks on rigid pavement performance using AASHTOWare pavement ME design. Road Materials and Pavement Design, 2024, vol. 25, no. 1, pp. 168–185. https://doi.org/10.1080/14680629.2023.2199879
- Rys D., Judycki J., Jaskula P. Analysis of effect of overloaded vehicles on fatigue life of flexible pavements based on weigh in motion (WIM) data. International Journal of Pavement Engineering, 2016, vol. 17, no. 8, pp. 716–726.https://doi.org/10.1080/10298436.2015.1019493
- Bekenov T.N., Mukhambetova A.I. Towards assessing the impact of the vehicle loads on the road surface wear. Proceedings of the XI international scientific-practice conference “Actual Problems of Transport And Energy: The Ways of Its Innovative Solutions”, 2023, pp. 124–127.(in Russian)
- Kamenchukov A.V., Kormilitsyna L.V., Lopashuk V.V., Tsupikova L.S. Influence of excess load on the wear and tear of the road surface. International Research Journal, 2021, no. 4-1(106), pp. 57–63. (in Russian). https://doi.org/10.23670/IRJ.2021.106.4.009
- Wang J., Wu M. An overview of research on weigh-in-motion system. Proc. of the Fifth World Congress on Intelligent Control and Automation (IEEE cat. no. 04EX788). V. 6, 2004, pp. 5241–5244. https://doi.org/10.1109/wcica.2004.1343721
- Brzozowski K., Maczyński A., Ryguła A., Konior T. A weigh-in-motion system with automatic data reliability estimation. Measurement, 2023, vol. 221, pp. 113494. https://doi.org/10.1016/j.measurement.2023.113494
- Szinyéri B., Kővári B., Völgyi I., Kollár D., Joó A.L. A strain gauge-based Bridge Weigh-In-Motion system using deep learning. Engineering Structures, 2023, vol. 277, pp. 115472.https://doi.org/10.1016/j.engstruct.2022.115472
- Sujon M., Dai F. Application of weigh-in-motion technologies for pavement and bridge response monitoring: State-of-the-art review. Automation in Construction, 2021, vol. 130, pp. 103844. https://doi.org/10.1016/j.autcon.2021.103844
- Adresi M., Abedi M., Dong W., Yekrangnia M. A review of different types of weigh-in-motion sensors: State-of-the-art. Measurement, 2024, vol. 225, pp. 114042. https://doi.org/10.1016/j.measurement.2023.114042
- Al-Tarawneh M., Huang Y., Lu P., Bridgelall R.Weigh-in-motion system in flexible pavements using fiber Bragg grating sensors part a: Concept. IEEE Transactions on Intelligent Transportation Systems, 2020, vol. 21, no. 12, pp. 5136–5147. https://doi.org/10.1109/tits.2019.2949242
- Wang K., Wei Z., Chen B., Cui H.-L. A fiber-optic weigh-in-motion sensor using fiber Bragg gratings. Proceedings of SPIE, 2005, vol. 6004, pp. 60040S. https://doi.org/10.1117/12.629372
- Alamandala S., Puth K., Sai Prasad R.L.N., Kumar P.R.FBG sensing system to study the bridge weigh-in-motion for measuring the vehicle parameters. Proc. of the 2018 3rd International Conference on Microwave and Photonics (ICMAP), 2018, pp. 1–2. https://doi.org/10.1109/icmap.2018.8354527
- Hill D., Nash P. Road traffic monitoring system. Patent US20040080432A1, 2004.
- Moor Ia.D., Varzhel S.V., Kozlova A.I., Dmitriev A.A., Savin V.V., Tokareva V.D.Sensitive element of fiber-optic sensor and method of dynamic measurement of speed, weight and distance between wheels of vehicles. Patent RU2816110C1, 2024. (in Russian)
- Kozlova A., Moor I., Varzhel S., Komisarov V., Kaliazina D., Savin V. Development and investigation of a method for measuring the speed and weight of moving objects using fiber Bragg gratings. Journal of Optical Technology, 2024, vol. 91, no. 4, pp. 242–246. https://doi.org/10.1364/JOT.91.000242
- Jeon S-J., Park S.Y., Kim S.T. Temperature compensation of fiber Bragg grating sensors in smart strand. Sensors, 2022, vol. 22, no. 9, pp. 3282. https://doi.org/10.3390/s22093282
- Velazquez-Carreon F., Perez-Alonzo A., Sandoval-Romero G.E. Temperature-compensated fiber Bragg grating sensor based on curvature sensing for bidirectional displacements measurement. Optical Fiber Technology, 2023, vol. 77, pp. 103257. https://doi.org/10.1016/j.yofte.2023.103257
- Dubovan J., Litvik J., Markovic M., Frniak M. Utilization of FBG’s in experimental weighing in motion systems. Proc. of the 2018 ELEKTRO, 2018, pp. 1–4. https://doi.org/10.1109/elektro.2018.8398252
- Wang J.-N., Tang J.-L. Using fiber bragg grating sensors to monitor pavement structures. Transportation Research Record: Journal of the Transportation Research Board, 2005, vol. 1913, no. 1. https://doi.org/10.1177/0361198105191300116
- Wang J., Han Y., Cao Z., Xu X., Zhang J., Xiao F. Applications of optical fiber sensor in pavement Engineering: A review. Construction and Building Materials, 2023, vol. 400, pp. 132713. https://doi.org/10.1016/j.conbuildmat.2023.132713
- Othonos A. Fiber Bragg gratings. Review of Scientific Instruments, 1997, vol. 68, no. 12, pp. 4309–4341. https://doi.org/10.1063/1.1148392
- Gribaev A.I., Pavlishin I.V., Stam A.M., Idrisov R.F., Varzhel S.V., Konnov K.A. Laboratory setup for fiber Bragg gratings inscription based on Talbot interferometer. Optical and Quantum Electronics, 2016, vol. 48, no. 12, pp. 540. https://doi.org/10.1007/s11082-016-0816-3
- Dmitriev A.A., Gribaev A.I., Varzhel S.V., Konnov K.A., Motorin E.A. High-performance fiber Bragg gratings arrays inscription method. Optical Fiber Technology, 2021, vol. 63, pp. 102508. https://doi.org/10.1016/j.yofte.2021.102508
- Fajkus M., Fridrich M., Nedoma J., Kahankova R., Martinek R., Bednar E., Kolarik J. PDMS-FBG-based fiber optic system for traffic monitoring in urban areas. IEEE Access, 2020, vol. 8, pp. 127648–127658.https://doi.org/10.1109/access.2020.3006985