Menu
Publications
2025
2024
2023
2022
2021
2020
2019
2018
2017
2016
2015
2014
2013
2012
2011
2010
2009
2008
2007
2006
2005
2004
2003
2002
2001
Editor-in-Chief
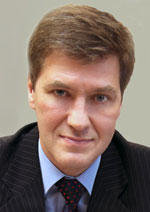
Nikiforov
Vladimir O.
D.Sc., Prof.
Partners
doi: 10.17586/2226-1494-2020-20-4-611-616
MESHLESS MODELING OF ELASTIC DEFORMATIONS OF POLYMERIC COMPOSITE MATERIALS UNDER STATIC LOADING
Read the full article

Article in Russian
For citation:
Abstract
For citation:
Sizaya A.V., Tsivilskiy I.V. Meshless modeling of elastic deformations of polymeric composite materials under static loading. Scientific and Technical Journal of Information Technologies, Mechanics and Optics, 2020, vol. 20, no. 4, pp. 611–616 (in Russian). doi: 10.17586/2226-1494-2020-20-4-611-616
Abstract
Subject of Research. Composites are unique materials combining lightness and strength, which makes them popular in the materials industry. Mathematical modeling of these materials is necessary to predict their behavior underspecific loads. The paper proposes a meshless method for mathematical modeling of anisotropic composite materials based on their representation as a set of meta-particles with spring-like bonds. Special feature of the presented work is the applicability of the same equations for the multi-scale modeling: on micro-scale (single fiber and an elementary volume of the compound) and macro-scale (cross-section of the whole composite part). Method. The method is based on Verlet-like time integration of particle displacements with consequent resolving of a system of elastic bonds with pre-calculated mass and stiffness. The method estimates temporal dynamics of composite deformations under applied mechanical load. The code for solution of motion equations and result visualization is written in pure JavaScript without any dependencies. Main Results. Elastic deformations of a simplified 2D model of carbon-fiber-reinforced plastic have been simulated (with a mixture of epoxy and polyester resins as a compound) under static mechanical load using the proposed method. Calculations on the micro-and macro-scales with different directions of fiber layering: at the angles of 0° and 90°. Flat layering type is selected. The results are verified via the ANSYS Composite PrepPost solver under equivalent conditions. The coincidence of the calculation results by the meta-particle method of the developed solver and the finite element method is 89 %. Practical Relevance. The results obtained can be used in the development of new types of composite materials at the modeling and forecasting stage, and can also allow simulations of composites taking into account micro-processes for exclusion of pore formation and other defects that cannot be resolved using macro-scale modeling.
Keywords: meshless methods, composite materials, structural dynamics, strength, mathematical modeling
References
References
1. Nienartowicz M., Strek T. Modeling and FEM analysis of dynamic properties of thermally optimal composite materials. Proc. 11th World Congress on Computational Mechanics, WCCM 2014, 5th European Conference on Computational Mechanics, ECCM 2014 and 6th European Conference on Computational Fluid Dynamics, ECFD 2014, 2014, pp. 593–604.
2. Sharma R., Mahajan P., Mittal R.K. Elastic modulus of 3D carbon/carbon composite using image-based finite element simulations and experiments. Composite Structures, 2013, vol. 98, pp. 69–78. doi: 10.1016/j.compstruct.2012.11.019
3. Xu K., Qian X. Microstructure analysis and multi-unit cell model of three dimensionally four-directional braided composites. Applied Composite Materials, 2014, vol. 22, no. 1, pp. 29–50. doi: 10.1007/s10443-014-9396-1
4. Raju B., Hiremath S.R., Mahapatra D.R. A review of micromechanics based models for effective elastic properties of reinforced polymer matrix composites. Composite Structures, 2018, vol. 204, pp. 607–619. doi: 10.1016/j.compstruct.2018.07.125
5. Swolfs Y., Verpoest I., Gorbatikh L. A review of input data and modelling assumptions in longitudinal strength models for unidirectional fibre-reinforced composites. Composite Structures, 2016, vol. 150, pp. 153–172. doi: 10.1016/j.compstruct.2016.05.002
6. Ghatage P.S., Kar V.R., Sudhagar P.E. On the numerical modelling and analysis of multi-directional functionally graded composite structures: A review. Composite Structures, 2020, vol. 236, pp. 111837. doi: 10.1016/j.compstruct.2019.111837
7. Dong K., Zhang J., Jin L., Gu B., Sun B. Multi-scale finite element analyses on the thermal conductive behaviors of 3D braided composites. Composite Structures, 2016, vol. 143, pp. 9–22. doi: 10.1016/j.compstruct.2016.02.029
8. Dong J., Huo N. A two-scale method for predicting the mechanical properties of 3D braided composites with internal defects. Composite Structures, 2016, vol. 152, pp. 1–10. doi: 10.1016/j.compstruct.2016.05.025
9. Zhang C., Curiel-Sosa J.L., Bui T.Q. A novel interface constitutive model for prediction of stiffness and strength in 3D braided composites. Composite Structures, 2017, vol. 163, pp. 32–43. doi: 10.1016/j.compstruct.2016.12.042
10. Bilisik K. Three-dimensional braiding for composites: A review. Textile Research Journal, 2013, vol. 83, no. 13, pp. 1414–1436. doi: 10.1177/0040517512450766
11. Shokrieh M.M., Mazloomi M.S. A new analytical model for calculation of stiffness of three-dimensional four-directional braided composites. Composite Structures, 2012, vol. 94, no. 3, pp. 1005–1015. doi: 10.1016/j.compstruct.2011.09.010
12. Gu Q., Quan Z., Yu J., Yan J., Sun B., Xu G. Structural modeling and mechanical characterizing of three-dimensional four-step braided composites: A review. Composite Structures, 2019, vol. 207, pp. 119–128. doi: 10.1016/j.compstruct.2018.09.065
13. Dandekar C.R., Shin Y.C. Modeling of machining of composite materials: A review. International Journal of Machine Tools & Manufacture, 2012, vol. 57, pp. 102–121. doi: 10.1016/j.ijmachtools.2012.01.006
14. Zhao G., Shu Q., Huang B. Numerical simulation of thermoplastic composite material by ANSYS. Advanced Materials Research, 2011, vol. 279, pp. 181–185. doi: 10.4028/www.scientific.net/AMR.279.181