Menu
Publications
2025
2024
2023
2022
2021
2020
2019
2018
2017
2016
2015
2014
2013
2012
2011
2010
2009
2008
2007
2006
2005
2004
2003
2002
2001
Editor-in-Chief
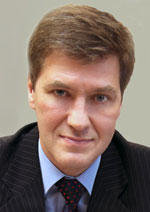
Nikiforov
Vladimir O.
D.Sc., Prof.
Partners
doi: 10.17586/2226-1494-2025-25-1-95-105
Multidimensional trajectory planning algorithm for a 5D printer slicer
Read the full article

Article in Russian
For citation:
Abstract
For citation:
Afanasev M.Ya., Solovev M.R., Krylova A.A., Shorohov S.A., Fedosov Yu.V. Multidimensional trajectory planning algorithm for a 5D printer slicer. Scientific and Technical Journal of Information Technologies, Mechanics and Optics, 2025, vol. 25, no. 1, pp. 95–105 (in Russian). doi: 10.17586/2226-1494-2025-25-1-95-105
Abstract
The article presents a trajectory planning algorithm for a 5D printer to solve problems that arise in traditional 3D printing. Standard 3D printing methods using layer-by-layer material deposition lead to anisotropy of mechanical properties, where the object strength depends on the direction of the layer application. This limits the ability to create isotropic- strength parts, especially those with complex geometry. The goal of the study is to develop an algorithm that enables uniform distribution of the mechanical properties of the object by optimizing the printing trajectories. The proposed algorithm is based on constructing trajectories using spherical spiral layers. The algorithm considers changing printing parameters, such as layer height and line thickness, and adapts to various geometric shapes of the object. A key feature is ensuring isotropy of the part properties by evenly distributing the material along the trajectories. The algorithm also includes the construction of normals at each point of the curve to accurately direct the movement of the printing head. This approach avoids the standard limitations typical of 3D printing. The algorithm was tested on various models, including simple and complex geometric shapes with high curvature. During computer modeling, experiments were conducted with different layer heights and line thicknesses, which allowed for the assessment of the influence of these parameters. The algorithm demonstrated high convergence under various input conditions, ensuring accurate trajectory execution regardless of initial parameters. The trajectories and normals were visualized, confirming the correct print direction and even material deposition. For further work convenience, an intermediate trajectory representation format was developed which is easily converted into G-codes. This allows data to be prepared for future physical experiments that will be conducted to assess the algorithm effectiveness in real printing conditions. The multidimensional trajectory planning algorithm opens up new possibilities for additive manufacturing, enabling the creation of complex objects with improved mechanical properties without the need for additional supports. The practical significance of the algorithm lies in its application in areas, such as aerospace, automotive, and medicine, where both complex geometric shapes and high part strength are important. Further research may focus on expanding the algorithm capabilities to work with various materials and adjusting printing parameters to improve the performance and quality of printed parts.
Keywords: 5D printing, multidimensional trajectories, slicing algorithm, additive manufacturing, trajectory planning, CNC path optimization
References
References
- Yigit I.E., Lazoglu I. Spherical slicing method and its application on robotic additive manufacturing. Progress in Additive Manufacturing, 2020, vol. 5, no. 4, pp. 387–394. https://doi.org/10.1007/s40964-020-00135-5
- Munasinghe N., Paul G. Radial slicing for helical-shaped advanced manufacturing applications. The International Journal of Advanced Manufacturing Technology, 2021, vol. 112, no. 3-4, pp. 1089–1100. https://doi.org/10.1007/s00170-020-05999-z
- Popov A.Y., Gushchin I.A., Drobotov A.V. Model preparation algorithm for 3D printing with discrete rotation. Proc. of the International Conference on Industrial Engineering, Applications and Manufacturing (ICIEAM), 2019, pp. 1–5. https://doi.org/10.1109/ICIEAM.2019.8742958
- Kaplan D., Rorberg S., Ben-Chen M., Sterman Y. NozMod: Nozzle Modification for efficient FDM 3D printing. Proc. of the 7th Annual ACM Symposium on Computational Fabrication, 2022, pp. 1–9. https://doi.org/10.1145/3559400.3561999
- Feng X., Cui B., Liu Y., Li L., Shi X., Zhang X. Curved-layered material extrusion modeling for thin-walled parts by a 5-axis machine. Rapid Prototyping Journal, 2021, vol. 27, no. 7, pp. 1378–1387. https://doi.org/10.1108/RPJ-11-2020-0272
- Insero F., Furlan V., Giberti H. Non-planar slicing for filled free-form geometries in robot-based FDM. Journal of Intelligent Manufacturing, 2023, in press. https://doi.org/10.1007/s10845-023-02250-w
- Liu B., Feng J., Lin Z., Wu S., He Y., Fu J. Spherical path planning for multi axis support free additive manufacturing of truss structures. Journal of Manufacturing Processes, 2024, vol. 109, pp. 198–212. https://doi.org/10.1016/j.jmapro.2023.12.011
- Mitropoulou I., Bernhard M., Dillenburger B. Print paths key-framing: design for non-planar layered robotic FDM printing. Proc. of the 5th Annual ACM symposium on computational fabrication, 2020, pp. 1–10. https://doi.org/10.1145/3424630.3425408
- Hong F., Hodges S., Myant C., Boyle D. Open5x: Accessible 5-axis 3D printing and conformal slicing. Extended Abstracts of the 2022 CHI Conference on Human Factors in Computing Systems, 2022, pp. 1–6. https://doi.org/10.1145/3491101.3519782
- Hong F., Lampret B., Myant C., Hodges S., Boyle D. 5-axis multi-material 3D printing of curved electrical traces. Additive Manufacturing, 2023, vol. 70, pp. 103546. https://doi.org/10.1016/j.addma.2023.103546
- Nayyeri P., Zareinia K., Bougherara H. Planar and nonplanar slicing algorithms for fused deposition modeling technology: A critical review. The International Journal of Advanced Manufacturing Technology, 2022, vol. 119, no. 5-6, pp. 2785–2810. https://doi.org/10.1007/s00170-021-08347-x
- Shan Y., Shui Y., Hua J., Mao H. Additive manufacturing of non-planar layers using isothermal surface slicing. Journal of Manufacturing Processes, 2023, vol. 86, pp. 326–335. https://doi.org/10.1016/j.jmapro.2022.12.054
- Neel T.L., Mesto T., Hascoet J.-Y. A novel slicing strategy for continuous printing with a helix 3D printer. Journal of Machine Engineering, 2022, vol. 22, no. 3, pp. 31–43. http://dx.doi.org/10.36897/jme/151119
- Tang J., Dong Y., Cai L., Zhu Q., Shi J. Conformal 3D printing algorithm for surfaces and its in situ repair applications. Micromachines, 2024, vol. 15, no. 7, pp. 920. https://doi.org/10.3390/mi15070920
- Nisja G.A., Cao A., Gao C. Short review of nonplanar fused deposition modeling printing. Material Design & Processing Communications, 2021, vol. 3, no. 4, pp. e221. https://doi.org/10.1002/mdp2.221
- Fortunato G.M., Nicoletta M., Batoni E., Vozzi G., De Maria C. A fully automatic non-planar slicing algorithm for the additive manufacturing of complex geometries. Additive Manufacturing, 2023, vol. 69, pp. 103541. https://doi.org/10.1016/j.addma.2023.103541
- Srinivas G.L., Laux M., Nair V.P., Brandstotter M. Multi-axis additive manufacturing: development of slicer and toolpath for 2.5 D/3D/5D printing. Advances in Service and Industrial Robotics, 2024, vol. 157, pp. 337–346. https://doi.org/10.1007/978-3-031-59257-7_34
- Alekseev A.A., Kirsanov A.E., Shishov O.V. 3D-PRINTING of ceramic products using spiral printing of the body of rotation with a wavy surface and the effect of "Weaving". Ogarev-online, 2020, no. 15 (152), pp. 1–8. (in Russian)
- Kirsanov A.E., Shishov O.V. 3D-PRINTING of ceramic products using spiral printing of the body of rotation with a wavy surface and the effect of "Weaving". Microelectronics and Computer Science. Proc. of the 27th All-Russian Interuniversity Conference of Students and Postgraduates: Abstracts. Moscow, MIET Publ., 2020, pp. 147. (in Russian)
- Kozlova A.D., Krauinsh P.Y. Synthesis of control algorithms desk 5D printer with parallel kinematics. Young Scientists Forum, 2018, no. 10 (26), pp. 573–576. (in Russian)
- Lebedev V.A., Solovjov V.P., Webb B.W. View factors of spherical, conic, and cylindrical spiral surfaces. Journal of Quantitative Spectroscopy and Radiative Transfer, 2021. vol. 274, pp. 107866. https://doi.org/10.1016/j.jqsrt.2021.107866
- Hüttig C., Stemmer K. The spiral grid: A new approach to discretize the sphere and its application to mantle convection. Geochemistry, Geophysics, Geosystems, 2008. vol. 9, no. 2, pp. Q02018. https://doi.org/10.1029/2007GC001581