Меню
Публикации
2025
2024
2023
2022
2021
2020
2019
2018
2017
2016
2015
2014
2013
2012
2011
2010
2009
2008
2007
2006
2005
2004
2003
2002
2001
Главный редактор
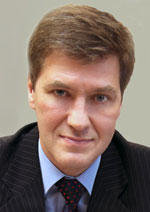
НИКИФОРОВ
Владимир Олегович
д.т.н., профессор
Партнеры
doi: 10.17586/2226-1494-2025-25-1-140-150
УДК 620.191, 629.017
Строкач Е.А., Пожидаев А.А.
Моделирование износа алюминиевого сплава частицами SiO2
Моделирование износа алюминиевого сплава частицами SiO2
Читать статью полностью

Язык статьи - русский
Ссылка для цитирования:
Аннотация
Ссылка для цитирования:
Строкач Е.А., Пожидаев А.А. Моделирование износа алюминиевого сплава частицами SiO2 // Научно-технический вестник информационных технологий, механики и оптики. 2025. Т. 25, № 1. С. 140–150. doi: 10.17586/2226-1494-2025-25-1-140-150
Аннотация
Введение. Современные методы моделирования процесса эрозии материалов твердыми частицами позволяют на микроуровне оценить влияние условий движения частиц, контакта с поверхностью, их формы и материала. Известные зарубежные работы по изучению пар эродента и алюминиевых, титановых сплавов и сталей не дают правильной оценки влияния трения и вращения частиц на остаточное напряженно-деформированное состояние и глубину износа при относительно высоких скоростях частиц. Мало изученным остается вопрос кратковременного нагрева приповерхностного слоя, что при высоких температурах может влиять на свойства материала. Устранение такой неопределенности повысит предиктивную точность модели абразивного износа. Метод. В работе представлены результаты двумерного конечно-элементного моделирования эрозионного износа поверхности распространенного алюминиевого сплава Al6061-T6 при взаимодействии с частицами двуокиси кремния (SiO2). Упругопластическое поведение материала поверхности и условия разрушения задавались моделью Джонсона–Кука. Основные результаты. Для оценки взаимовлияния следов множественных ударов частиц и изменения напряженно-деформированного состояния поверхности выполнено моделирование последовательных ударов трех групп жестких частиц диаметром 250 мкм со скоростью 155 м/с под углом 45°. Изучено изменение эквивалентных напряжений в образце после каждого удара. Проведена оценка влияния трения между частицами SiO2 и поверхностью, а также вращения сферических частиц и его направления. Обсуждение. Показано, что учет трения влияет на профиль эквивалентных напряжений уже после первого удара и сохраняет влияние в дальнейшем. Зависимость результатов от направления вращения частиц при скорости 1000 об/мин проявляется только после второго удара и усиливается после удара третьей группы частиц. Предполагается, что для алюминиевых сплавов серии 6000 и сферических частиц SiO2 другого размера полученные зависимости будут качественно сохраняться. Дальнейшие исследования предполагают анализ влияния формы несферических частиц SiO2 при вращении, важность учета деформируемости частиц при ударе, а также воздействие этих эффектов при большем количестве ударов и различных условиях контакта.
Ключевые слова: эрозия твердыми частицами, абразивный износ, FEA-моделирование эрозии, ANSYS Explicit, остаточные напряжения, модель Джонсона–Кука, Al6061
Благодарности. Работа выполнена в рамках государственного задания Министерства науки и высшего образования Российской Федерации, тема № FSFF-2023-0006.
Список литературы
Благодарности. Работа выполнена в рамках государственного задания Министерства науки и высшего образования Российской Федерации, тема № FSFF-2023-0006.
Список литературы
- Боркова А.Н. Эрозионная стойкость авиационных материалов при соударении с твердыми (пылевыми) частицами: автореферат диссертации на соискание ученой степени кандидата технических наук / Всероссийский НИИ авиационных материалов. М., 2006. 26 с.
- Клейс И.Р. Некоторые исследования по абразивной эрозии: диссертация на соискание ученой степени доктора технических наук / МИНХиГП им. И.М. Губкина. М., 1970. 250 с.
- Крамченков Е.М. Исследование эрозионного изнашивания материалов: автореферат диссертации на соискание ученой степени кандидата технических наук / ГАНГ им. И.М. Губкина. М., 1995. 26 с.
- Строкач Е.А., Кожевников Г.Д., Пожидаев А.А., Добровольский С.В. Моделирование эрозионного износа титанового сплава высокоскоростным потоком частиц // Обработка металлов (технология, оборудование, инструменты). 2023. Т. 25. № 4. С. 268–283. https://doi.org/10.17212/1994-6309-2023-25.4-268-283
- Строкач Е.А., Кожевников Г.Д., Пожидаев А.А. Численное моделирование процесса эродирования твердыми частицами в газовом потоке (обзор) // Вестник ПНИПУ. Аэрокосмическая техника. 2021. № 67. С. 56–69. https://doi.org/10.15593/2224-9982/2021.67.06
- Liu Y., Cao Z., Yuan J., Sun X., Su H., Wang L. Effect of morphology, impact velocity and angle of the CaO-MgO-Al2O3-SiO2 (CMAS) particle on the erosion behavior of Thermal Barrier Coatings (TBCs): a finite element simulation study // Coatings. 2022. V. 12. N 5. P. 576. https://doi.org/10.3390/coatings12050576
- Ma Z.S., Fu L.H., Yang L., Zhou Y.C., Lu C. Finite Element Simulations on Erosion and Crack Propagation in Thermal Barrier Coatings // High Temperature Materials and Processes. 2015. V. 34. N 4. P. 387–393. https://doi.org/10.1515/htmp-2014-0068
- Oviedo F., Valarezo A. Residual stress in high-velocity impact coatings: parametric finite element analysis approach // Journal of Thermal Spray Technology. 2020. V. 29. N 6. P. 1268–1288. https://doi.org/10.1007/s11666-020-01026-5
- Liu Z.G., Wan S., Nguyen V.B., Zhang Y.W. Finite element analysis of erosive wear for offshore structure // Proc. of the 13th International Conference on Fracture. 2013. P. 461–468.
- ElTobgy M.S., Ng E., Elbestawi M.A. Finite element modeling of erosive wear // International Journal of Machine Tools and Manufacture. 2005. V. 45. N 11. P. 1337–1346. https://doi.org/10.1016/j.ijmachtools.2005.01.007
- Singh P.K., Hota A.R., Mishra S.B. Finite element modelling of erosion parameters in boiler components // Asian Journal of Engineering and Applied Technology. 2018. V. 7. N S2. P. 12–16. https://doi.org/10.51983/ajeat-2018.7.2.964
- Du M., Li Z., Feng L., Dong X., Che J., Zhang Y. Numerical simulation of particle fracture and surface erosion due to single particle impact // AIP Advances. 2021. V. 11. N 3. P. 035218. https://doi.org/10.1063/5.0042928
- Evans A.G., Gulden M.E., Rosenblatt M. Impact damage in brittle materials in the elastic-plastic response régime // Proc. of the Royal Society A: Mathematical, Physical and Engineering sciences. 1978. V. 361. N 1706. P. 343–365. https://doi.org/10.1098/rspa.1978.0106
- Mohammadi B., Khoddami A. Representative volume element-based simulation of multiple solid particles erosion of a compressor blade considering temperature effect // Proceedings of the Institution of Mechanical Engineers, Part J: Journal of Engineering Tribology. 2020. V. 234. N 8. P. 1173–1184. https://doi.org/10.1177/1350650119884825
- Taherkhani B., Anaraki A.P., Kadkhodapour J., Farahani N., Tu H. Erosion due to solid particle impact on the turbine blade: experiment and simulation // Journal of Failure Analysis and Prevention. 2019. V. 19. N 6. P. 1739–1744. https://doi.org/10.1007/s11668-019-00775-y
- Wu B., Wu F., Li J. Finite Element Modeling of Correlating Mechanical Properties with Erosion Wear Rate // Proc. of the 3rd International Conference on Electrical, Automation and Mechanical Engineering (EAME 2018). 2018. P. 273–276. https://doi.org/10.2991/eame-18.2018.57
- Khoddami A.S., Salimi-Majd D., Mohammadi B. Finite element and experimental investigation of multiple solid particle erosion on Ti-6Al-4V titanium alloy coated by multilayer wear-resistant coating // Surface and Coatings Technology. 2019. V. 372. P. 173–189. https://doi.org/10.1016/j.surfcoat.2019.05.042
- Petrov Y.V., Bragov A.M., Kazarinov N.A., Evstifeev A.D. Experimental and numerical analysis of the highspeed deformation and erosion damage of the titanium alloy VT-6 // Physics of the Solid State. 2017. V. 59. N 1. P. 93–97. https://doi.org/10.1134/S1063783417010267
- Balu P., Kong F., Hamid S., Kovacevic R. Finite element modeling of solid particle erosion in AISI 4140 steel and nickel–tungsten carbide composite material produced by the laser-based powder deposition process // Tribology International. 2013. V. 62. P. 18–28. https://doi.org/10.1016/j.triboint.2013.01.021
- Liu Z.G., Wan S., Nguyen V.B., Zhang Y.W. A numerical study on the effect of particle shape on the erosion of ductile materials // Wear. 2014. V. 313. N 1–2. P. 135–142. https://doi.org/10.1016/j.wear.2014.03.005
- Zhang H., Dong X. Finite element analysis of multiple solid particles erosion in cermet coating // Surface and Coatings Technology. 2015. V. 262. P. 184–190. https://doi.org/10.1016/j.surfcoat.2014.12.040
- Mei Y., Dong X. Angular particle impact on ductile materials using the Lagrangian gradient smoothing method // Tribology Transactions. 2021. V. 64. N 6. P. 1149–1165. https://doi.org/10.1080/10402004.2021.1944709
- Zheng C., Liu Y., Chen C., Qin J., Ji R., Cai B. Numerical study of impact erosion of multiple solid particle // Applied Surface Science. 2017. V. 423. P. 176–184. https://doi.org/10.1016/j.apsusc.2017.06.132
- Zang X., Cao X., Xie Z., Zhang J., Darihaki F., Liu Y. Surface deformation under overlapping impacts of solid particles // Friction. 2023. V. 11. N 2. P. 280–301. https://doi.org/10.1007/s40544-021-0600-2
- Chen J., He G., Han Y., Yuan Z., Li Z., Zhang Z., Han X., Yan S. Structural toughness and interfacial effects of multilayer TiN erosion-resistant coatings based on high strain rate repeated impact loads // Ceramics International. 2021. V. 47. N 19. P. 27660–27667. https://doi.org/10.1016/j.ceramint.2021.06.190
- Di J., Wang S., Zhang L., Cai L., Xie Y. Study on the erosion characteristics of boride coatings by finite element analysis // Surface and Coatings Technology. 2018. V. 333. P. 115–124. https://doi.org/10.1016/j.surfcoat.2017.10.042
- Yu Q.M., He Q., Ning F.L. Influence of interface morphology on erosion failure of thermal barrier coatings // Ceramics International. 2018. V. 44. N 17. P. 21349–21357. https://doi.org/10.1016/j.ceramint.2018.08.188
- Zhang H., Li Z., He W., Liao B., He G., Cao X., Li Y. Damage evolution and mechanism of TiN/Ti multilayer coatings in sand erosion condition // Surface and Coatings Technology. 2018. V. 353. P. 210–220. https://doi.org/10.1016/j.surfcoat.2018.08.062
- Fang Z., Chen J., He W., Yang Z., Yuan Z., Geng M., He G. Study on the damage mechanism of TiN/Ti coatings based on multi-directional impact // Coatings. 2019. V. 9. N 11. P. 765. https://doi.org/10.3390/coatings9110765
- Lesnevskiy L.N., Lyakhovetskiy M.A, Kozhevnikov G.D. Ushakov A.M. Research of the AK4-1 alloy microarc oxidation modes effect on the composite ceramic coatings erosion resistance // Journal of Physics: Conference Series. 2019. V. 1281. N 1. P. 012048. https://doi.org/10.1088/1742-6596/1281/1/012048
- Гурин В.Г. Исследование процессов разрушения при высокоскоростной эрозии материалов: дипломная работаю СПб., 2017 [Электронный ресурс]. https://dspace.spbu.ru/bitstream/11701/10536/1/tekst_diploma.pdf (дата обращения: 05.01.2023).
- Tarodiya R., Levy A. Surface erosion due to particle-surface interactions - A review // Powder Technology. 2021. V. 387. P. 527–559. https://doi.org/10.1016/j.powtec.2021.04.055
- ANSYS Explicit Dynamics Analysis Guide. Release 2020 R2, July 2020.
- Wilkins M.L. Calculation of Elastic-plastic Flow. Lawrence Livermore Laboratory, University of California, 1969. 99 p.
- Li Q, Jing L, Sun Q, Ji L., Chen S. The finite element modeling of the impacting process of hard particles on pump components // Open Physics. 2022. V. 20. N 1. P. 596–608. https://doi.org/10.1515/phys-2022-0048
- Dong X., Li Z., Zhang Q., Zeng W., Liu GR. Analysis of surface-erosion mechanism due to impacts of freely rotating angular particles using smoothed particle hydrodynamics erosion model // Proceedings of the Institution of Mechanical Engineers, Part J: Journal of Engineering Tribology. 2017. V. 231. N 12. P. 1537–1551. https://doi.org/10.1177/1350650117700
- Zheng C., Liu Y., Chen C., Qin J., Zhang S. Finite element analysis on the dynamic erosion process using multiple-particle impact model // Powder Technology. 2017. V. 315. P. 163–170. https://doi.org/10.1016/j.powtec.2017.04.016
- Hadavi V., Moreno C.E., Papini M. Numerical and experimental analysis of particle fracture during solid particle erosion, part I: Modeling and experimental verification // Wear. 2016. V. 356–357. P. 135–145. https://doi.org/10.1016/j.wear.2016.03.008
- Abubakar A.A., Arif A.F.M., Akhtar S.S., Mostaghimi J. Splats formation, interaction and residual stress evolution in thermal spray coating using a hybrid computational model // Journal of Thermal Spray Technology. 2019. V. 28. N 3. P. 359–377. https://doi.org/10.1007/s11666-019-00828-6
- Dong X., Li Z., Feng L., Sun Z., Fan C. Modeling, simulation, and analysis of the impact(s) of single angular-type particles on ductile surfaces using smoothed particle hydrodynamics // Powder Technology. 2017. V. 318. P. 363–382. https://doi.org/10.1016/j.powtec.2017.06.011
- Урбанович JI.И., Крамченков Е.М., Чуносов Ю.Н. Разогрев твердого тела в зоне удара эродирующей твердой частицы // Трение и износ. 1994. Т. 15. № 6. С. 965–972.
- Chowdhury M.A., Debnath U.K., Nuruzzaman D.M., Islam M.M. Experimental analysis of aluminum alloy under solid particle erosion process // Proceedings of the Institution of Mechanical Engineers, Part J: Journal of Engineering Tribology. 2016. V. 230. N12. P. 1516–1541. https://doi.org/10.1177/1350650116639466
- Finnie I. Erosion of surfaces by solid particles Oberflächenerosion durch feste teilchen // Wear. 1960. V. 3. N 2. P. 87–103. https://doi.org/10.1016/0043-1648(60)90055-7
- Oka Y.I., Yoshida T. Practical estimation of erosion damage caused by solid particle impact: Part 2: Mechanical properties of materials directly associated with erosion damage // Wear. 2005. V. 259. N 1-6. P. 102–109. https://doi.org/10.1016/j.wear.2005.01.040
- ANSYS Fluent Theory Guide. Canonsburg, PA: ANSYS Inc, 2022. 1080 p.
- Laguna-Camacho J., Martínez-García H., Escamilla-Rodríguez F., Alarcón-Rosas C., Calderón-Ramón C., Ríos-Velasco L., Pelcastre-Lozano M., Casados-Sánchez Á., González-Gómez M. Erosion Behavior of AISI 6061-T6 // Journal of Surface Engineered Materials and Advanced Technology. 2015. V. 5. P. 136–146. https://doi.org/10.4236/jsemat.2015.53015
- Тхабисимов А.Б. Повышение абразивной стойкости лопаточного аппарата первых ступеней цилиндров высокого и среднего давления мощных паровых турбин: диссертация на соискание ученой степени кандидата технических наук / Национальный исследовательский университет МЭИ. М., 2016. 179 с.
- Петров Ю.В., Атрошенко С.А., Казаринов Н.А., Евстифеев А.Д., Соловьев В.Ю. Динамическое разрушение поверхности сплава алюминия в условиях высокоскоростной эрозии // Физика твердого тела. 2017. Т. 59. № 4. С. 648-652. https://doi.org/10.21883/FTT.2017.04.44264.173
- Евстифеев А.Д., Смирнов И.В. Особенности эрозионного разрушения металлических материалов при воздействии потока твердых частиц // Физическая мезомеханика. 2021. Т. 24. № 2. С. 5–12. https://doi.org/10.24412/1683-805X-2021-2-5-12
- Евстифеев А.Д., Смирнов И.В., Петров Ю.В. Влияние динамической прочности материала на его эрозионную стойкость // Физика твердого тела. 2020. Т. 62. № 10. С. 1569–1572. https://doi.org/10.21883/FTT.2020.10.49897.088
- Sezer H., Fidan S. Solid Particle Erosion Effects On Surface Plastic Deformation Of Alüminum Alloy // El-Cezerî Journal of Science and Engineering. 2018. V. 5. N 1. P. 243–250. https://doi.org/10.31202/ecjse.364685