Menu
Publications
2025
2024
2023
2022
2021
2020
2019
2018
2017
2016
2015
2014
2013
2012
2011
2010
2009
2008
2007
2006
2005
2004
2003
2002
2001
Editor-in-Chief
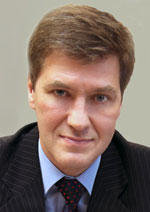
Nikiforov
Vladimir O.
D.Sc., Prof.
Partners
doi: 10.17586/2226-1494-2025-25-1-140-150
Numerical study of SiO2 particle erosion of an aluminum alloy
Read the full article

Article in Russian
For citation:
Abstract
For citation:
Strokach E.A., Pozhidaev A.A. Numerical study of SiO2 particle erosion of an aluminum alloy. Scientific and Technical Journal of Information Technologies, Mechanics and Optics, 2025, vol. 25, no. 1, pp. 140–150 (in Russian). doi: 10.17586/2226-1494-2025-25-1-140-150
Abstract
Computational methods used to simulate solid particle erosion have advanced so far being able to estimate partial effect of various processing factors on microlevel, such as particle-surface contact, its particle material, and shape, etc. The published activities taken to study different effects in this aspect for popular aluminium or titanium alloys and steels still have a gap in knowledge addressing some process parameters. The influence of particle rotation and its direction on stress-strain state and wear depth is still understudied. The impact of friction consideration in relatively high-speed contacts should also be studied, as well as the surface layer heating effect which may influence the material strength properties when the temperatures get high. Understanding these effects would increase the predictive ability of the erosion model and its accuracy — which is presented in our 2D simulation study for SiO2 solid particles and a widespread Al6061-T6 alloy. The elastic-plastic and failure properties of the surface material were presented by the Johnson-Cook model. To estimate the influence of multiple impacts on the stress-strain state, three sequential rigid impacts of 250 µm particles at 45° and 155 m/s were modeled. Main attention was driven to the evolution of equivalent von-Mises stresses in the sample after each impact and its dependence on the friction and rotation of particles. It was shown that the effect of friction can be noticed after the first impact, remaining high throughout the simulation. Whereas the influence of rotation direction at 1000 rpm was noticeable after the second impact and tended to increase after the third impact. It is assumed that for other 6000 series aluminium alloys being eroded by spherical SiO2 particles with differing diameters the erosive behavior would keep. However, future studies should be addressed to the analyzing of non-spherical particles rotation, consideration of particle deformation, and to studies of these parameters including more impacts and different contact properties in complex.
Keywords: solid particle erosion, abrasive wear, FEA erosion simulation, ANSYS Explicit, residual stresses, Johnson-Cook model, Al6061
Acknowledgements. The work was funded by the Ministry of Science and Higher Education of the Russian Federation, grant No. FSFF- 2023-0006.
References
Acknowledgements. The work was funded by the Ministry of Science and Higher Education of the Russian Federation, grant No. FSFF- 2023-0006.
References
- Borkova A.N. Erosion resistance of the aircraft materials upon collision with solid (dust) particles. Abstract of a dissertation for the degree of candidate of technical sciences. Moscow, 2006, 26 p. (in Russian)
- Kleis I.R. Some research on abrasive erosion. Dissertation for the degree of doctor of technical sciences. Moscow, 1970, 250 p. (in Russian)
- Kramchenkov E.M. Investigation of the erosive wear of materials. Abstract of a dissertation for the degree of candidate of technical sciences. Moscow, 1995, 26 p. (in Russian)
- Strokach E., Kozhevnikov G., Pozhidaev A., Dobrovolsky S. Numerical study of titanium alloy high-velocity solid particle erosion. Obrabotka metallov-Metal Working and Material Science, 2023, vol. 25, no. 4, pp. 268-283. https://doi.org/10.17212/1994-6309-2023-25.4-268-283
- Strokach E., Kozhevnikov G., Pozhidaev A. Numerical simulation of solid particle erosion in a gaseous flow (review). Vestnik PNIPU. Ajerokosmicheskaja tehnika, 2021, no. 67, pp. 56–69. (in Russian). https://doi.org/10.15593/2224-9982/2021.67.06
- Liu Y., Cao Z., Yuan J., Sun X., Su H., Wang L. Effect of morphology, impact velocity and angle of the CaO-MgO-Al2O3-SiO2 (CMAS) particle on the erosion behavior of Thermal Barrier Coatings (TBCs): a finite element simulation study. Coatings, 2022, vol. 12, no. 5, pp. 576. https://doi.org/10.3390/coatings12050576
- Ma Z.S., Fu L.H., Yang L., Zhou Y.C., Lu C. Finite Element Simulations on Erosion and Crack Propagation in Thermal Barrier Coatings. High Temperature Materials and Processes, 2015, vol. 34, no. 4, pp. 387–393. https://doi.org/10.1515/htmp-2014-0068
- Oviedo F., Valarezo A. Residual stress in high-velocity impact coatings: parametric finite element analysis approach. Journal of Thermal Spray Technology, 2020, vol. 29, no 6, pp. 1268–1288. https://doi.org/10.1007/s11666-020-01026-5
- Liu Z.G., Wan S., Nguyen V.B., Zhang Y.W. Finite element analysis of erosive wear for offshore structure. Proc. of the 13th International Conference on Fracture, 2013, pp. 461–468.
- ElTobgy M.S., Ng E., Elbestawi M.A. Finite element modeling of erosive wear. International Journal of Machine Tools and Manufacture, 2005, vol. 45, no. 11, pp. 1337–1346. https://doi.org/10.1016/j.ijmachtools.2005.01.007
- Singh P.K., Hota A.R., Mishra S.B. Finite element modelling of erosion parameters in boiler components. Asian Journal of Engineering and Applied Technology, 2018, vol. 7, no. S2, pp. 12–16. https://doi.org/10.51983/ajeat-2018.7.2.964
- Du M., Li Z., Feng L., Dong X., Che J., Zhang Y. Numerical simulation of particle fracture and surface erosion due to single particle impact. AIP Advances, 2021, vol. 11, no. 3, pp. 035218. https://doi.org/10.1063/5.0042928
- Evans A.G., Gulden M.E., Rosenblatt M. Impact damage in brittle materials in the elastic-plastic response régime. Proc. of the Royal Society A: Mathematical, Physical and Engineering sciences, 1978, vol. 361, no. 1706, pp. 343–365. https://doi.org/10.1098/rspa.1978.0106
- Mohammadi B., Khoddami A. Representative volume element-based simulation of multiple solid particles erosion of a compressor blade considering temperature effect. Proceedings of the Institution of Mechanical Engineers, Part J: Journal of Engineering Tribology, 2020, vol. 234, no. 8. pp. 1173–1184. https://doi.org/10.1177/1350650119884825
- Taherkhani B., Anaraki A.P., Kadkhodapour J., Farahani N., Tu H. Erosion due to solid particle impact on the turbine blade: experiment and simulation. Journal of Failure Analysis and Prevention, 2019, vol. 19, no. 6, pp. 1739–1744. https://doi.org/10.1007/s11668-019-00775-y
- Wu B., Wu F., Li J. Finite Element Modeling of Correlating Mechanical Properties with Erosion Wear Rate. Proc. of the 3rd International Conference on Electrical, Automation and Mechanical Engineering (EAME 2018), 2018, pp. 273–276. https://doi.org/10.2991/eame-18.2018.57
- Khoddami A.S., Salimi-Majd D., Mohammadi B. Finite element and experimental investigation of multiple solid particle erosion on Ti-6Al-4V titanium alloy coated by multilayer wear-resistant coating. Surface and Coatings Technology, 2019, vol. 372. pp. 173–189. https://doi.org/10.1016/j.surfcoat.2019.05.042
- Petrov Y.V., Bragov A.M., Kazarinov N.A., Evstifeev A.D. Experimental and numerical analysis of the highspeed deformation and erosion damage of the titanium alloy VT-6. Physics of the Solid State, 2017, vol. 59, no. 1, pp. 93–97. https://doi.org/10.1134/S1063783417010267
- Balu P., Kong F., Hamid S., Kovacevic R. Finite element modeling of solid particle erosion in AISI 4140 steel and nickel–tungsten carbide composite material produced by the laser-based powder deposition process. Tribology International, 2013, vol. 62, pp. 18–28. https://doi.org/10.1016/j.triboint.2013.01.021
- Liu Z.G., Wan S., Nguyen V.B., Zhang Y.W. A numerical study on the effect of particle shape on the erosion of ductile materials. Wear, 2014, vol. 313, no. 1–2, pp. 135–142. https://doi.org/10.1016/j.wear.2014.03.005
- Zhang H., Dong X. Finite element analysis of multiple solid particles erosion in cermet coating. Surface and Coatings Technology, 2015, vol. 262, pp. 184–190. https://doi.org/10.1016/j.surfcoat.2014.12.040
- Mei Y., Dong X. Angular particle impact on ductile materials using the Lagrangian gradient smoothing method. Tribology Transactions, 2021, vol. 64, no. 6, pp. 1149–1165. https://doi.org/10.1080/10402004.2021.1944709
- Zheng C., Liu Y., Chen C., Qin J., Ji R., Cai B. Numerical study of impact erosion of multiple solid particle. Applied Surface Science, 2017, vol. 423, pp. 176–184. https://doi.org/10.1016/j.apsusc.2017.06.132
- Zang X., Cao X., Xie Z., Zhang J., Darihaki F., Liu Y. Surface deformation under overlapping impacts of solid particles. Friction. 2023, vol. 11, no. 2, pp. 280–301. https://doi.org/10.1007/s40544-021-0600-2
- Chen J., He G., Han Y., Yuan Z., Li Z., Zhang Z., Han X., Yan S. Structural toughness and interfacial effects of multilayer TiN erosion-resistant coatings based on high strain rate repeated impact loads. Ceramics International, 2021, vol. 47, no. 19, pp. 27660–27667. https://doi.org/10.1016/j.ceramint.2021.06.190
- Di J., Wang S., Zhang L., Cai L., Xie Y. Study on the erosion characteristics of boride coatings by finite element analysis. Surface and Coatings Technology, 2018, vol. 333, pp. 115–124. https://doi.org/10.1016/j.surfcoat.2017.10.042
- Yu Q.M., He Q., Ning F.L. Influence of interface morphology on erosion failure of thermal barrier coatings. Ceramics International, 2018, vol. 44, N 17, pp. 21349–21357. https://doi.org/10.1016/j.ceramint.2018.08.188
- Zhang H., Li Z., He W., Liao B., He G., Cao X., Li Y. Damage evolution and mechanism of TiN/Ti multilayer coatings in sand erosion condition. Surface and Coatings Technology, 2018, vol. 353, pp. 210–220. https://doi.org/10.1016/j.surfcoat.2018.08.062
- Fang Z., Chen J., He W., Yang Z., Yuan Z., Geng M., He G. Study on the damage mechanism of TiN/Ti coatings based on multi-directional impact. Coatings, 2019, vol. 9, no. 11, pp. 765. https://doi.org/10.3390/coatings9110765
- Lesnevskiy L.N., Lyakhovetskiy M.A, Kozhevnikov G.D. Ushakov A.M. Research of the AK4-1 alloy microarc oxidation modes effect on the composite ceramic coatings erosion resistance. Journal of Physics: Conference Series, 201, vol. 1281, no. 1, pp. 012048. https://doi.org/10.1088/1742-6596/1281/1/012048
- Gurin V. Investigation of fracture processes at high-rate erosion of materials. Graduation Thesis. St. Petersburg, 2017. Available: https://dspace.spbu.ru/bitstream/11701/10536/1/tekst_diploma.pdf (accessed: 05.01.2023). (in Russian)
- Tarodiya R., Levy A. Surface erosion due to particle-surface interactions - A review // Powder Technology, 2021, vol. 387, pp. 527–559. https://doi.org/10.1016/j.powtec.2021.04.055
- ANSYS Explicit Dynamics Analysis Guide, Release 2020 R2, July 2020.
- Wilkins M.L. Calculation of Elastic-plastic Flow. Lawrence Livermore Laboratory, University of California, 1969, 99 p.
- Li Q, Jing L, Sun Q, Ji L., Chen S. The finite element modeling of the impacting process of hard particles on pump components. Open Physics, 2022, vol. 20, no. 1, pp. 596–608. https://doi.org/10.1515/phys-2022-0048
- Dong X., Li Z., Zhang Q., Zeng W., Liu GR. Analysis of surface-erosion mechanism due to impacts of freely rotating angular particles using smoothed particle hydrodynamics erosion model. Proceedings of the Institution of Mechanical Engineers, Part J: Journal of Engineering Tribology, 2017, vol. 231, no. 12, pp. 1537–1551. https://doi.org/10.1177/1350650117700
- Zheng C., Liu Y., Chen C., Qin J., Zhang S. Finite element analysis on the dynamic erosion process using multiple-particle impact model. Powder Technology, 2017, vol. 315, pp. 163–170. https://doi.org/10.1016/j.powtec.2017.04.016
- Hadavi V., Moreno C.E., Papini M. Numerical and experimental analysis of particle fracture during solid particle erosion, part I: Modeling and experimental verification. Wear, 2016, vol. 356–357, pp. 135–145. https://doi.org/10.1016/j.wear.2016.03.008
- Abubakar A.A., Arif A.F.M., Akhtar S.S., Mostaghimi J. Splats formation, interaction and residual stress evolution in thermal spray coating using a hybrid computational model. Journal of Thermal Spray Technology, 2019, vol. 28, no. 3, pp. 359–377. https://doi.org/10.1007/s11666-019-00828-6
- Dong X., Li Z., Feng L., Sun Z., Fan C. Modeling, simulation, and analysis of the impact(s) of single angular-type particles on ductile surfaces using smoothed particle hydrodynamics. Powder Technology, 2017, vol. 318, pp. 363–382. https://doi.org/10.1016/j.powtec.2017.06.011
- Urbanovich L.I., Kramchenkov E.M., Chunosov Iu.N. Solid body heating in the impact zone of an eroding solid particle. Trenie i Iznos, 1994, vol. 15, no. 6, pp. 965-972. (in Russian)
- Chowdhury M.A., Debnath U.K., Nuruzzaman D.M., Islam M.M. Experimental analysis of aluminum alloy under solid particle erosion process. Proceedings of the Institution of Mechanical Engineers, Part J: Journal of Engineering Tribology, 2016, vol. 230, no. 12, pp. 1516–1541. https://doi.org/10.1177/1350650116639466
- Finnie I. Erosion of surfaces by solid particles Oberflächenerosion durch feste teilchen. Wear, 1960, vol. 3, no. 2, pp. 87–103. https://doi.org/10.1016/0043-1648(60)90055-7
- Oka Y.I., Yoshida T. Practical estimation of erosion damage caused by solid particle impact: Part 2: Mechanical properties of materials directly associated with erosion damage. Wear, 2005, vol. 259, no. 1-6, pp. 102–109. https://doi.org/10.1016/j.wear.2005.01.040
- ANSYS Fluent Theory Guide. Canonsburg, PA: ANSYS Inc, 2022. 1080 p.
- Laguna-Camacho J., Martínez-García H., Escamilla-Rodríguez F., Alarcón-Rosas C., Calderón-Ramón C., Ríos-Velasco L., Pelcastre-Lozano M., Casados-Sánchez Á., González-Gómez M. Erosion Behavior of AISI 6061-T6. Journal of Surface Engineered Materials and Advanced Technology, 2015, vol. 5, pp. 136–146. https://doi.org/10.4236/jsemat.2015.53015
- Tkhabisimov A.B. Improving the the blade apparatus abrasive resistance at the first stages of high and medium pressure cylinders of the powerful steam turbines. Dissertation for the degree of candidate of technical sciences. Moscow, 2016, 179 p. (in Russian)
- Petrov Y.V., Atroshenko S.A., Kazarinov N.A., Evstifeev A.D., Solov'ev V.Y. Dynamic fracture of the surface of an aluminum alloy under conditions of high-speed erosion. Physics of the Solid State, 2017, vol.59, no. 4, pp. 661-666. https://doi.org/10.1134/S1063783417040175
- Evstifeev A.D., Smirnov I.V. Features of Solid Particle Erosion of Metals. Physical Mesomechanics, 2022, vol. 25, n. 1, pp. 12-17. https://doi.org/10.1134/S1029959922010027.
- Evstifeev A.D., Smirnov I.V., Petrov Y.V. Effect of Dynamic Strength of a Material on Its Erosion Resistance. Physics of the Solid State, 2020, vol. 62, no. 10, pp. 1737-1740. https://doi.org/10.1134/S1063783420100066
- Sezer H., Fidan S. Solid Particle Erosion Effects On Surface Plastic Deformation Of Alüminum Alloy. El-Cezerî Journal of Science and Engineering, 2018, vol. 5, no. 1, pp. 243–250. https://doi.org/10.31202/ecjse.364685