Menu
Publications
2025
2024
2023
2022
2021
2020
2019
2018
2017
2016
2015
2014
2013
2012
2011
2010
2009
2008
2007
2006
2005
2004
2003
2002
2001
Editor-in-Chief
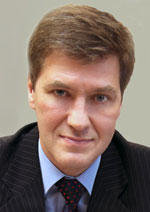
Nikiforov
Vladimir O.
D.Sc., Prof.
Partners
MODELING OF MANUFACTURING ERRORS FOR PIN-GEAR ELEMENTS OF PLANETARY GEARBOX
Read the full article

Article in Russian
For citation: Работа подготовлена по результатам НИОКРТ «Создание высокотехнологичного производства прецизионных быстродействующих силовых электромеханических приводов нового поколения» в Университете ИТМО, при финансовой поддержке Министерства образования и науки Российской Федерации согласно постановлению Правительства Российской Федерации от 9 апреля 2010 г. № 218 «О мерах государственной поддержки развития кооперации российских высших учебных заведений, государственных научных учреждений и организаций, реализующих комплексные проекты по созданию высокотехнологичного производства».
Abstract
For citation: Работа подготовлена по результатам НИОКРТ «Создание высокотехнологичного производства прецизионных быстродействующих силовых электромеханических приводов нового поколения» в Университете ИТМО, при финансовой поддержке Министерства образования и науки Российской Федерации согласно постановлению Правительства Российской Федерации от 9 апреля 2010 г. № 218 «О мерах государственной поддержки развития кооперации российских высших учебных заведений, государственных научных учреждений и организаций, реализующих комплексные проекты по созданию высокотехнологичного производства».
Abstract
Theoretical background for calculation of k-h-v type cycloid reducers was developed relatively long ago. However, recently the matters of cycloid reducer design again attracted heightened attention. The reason for that is that such devices are used in many complex engineering systems, particularly, in mechatronic and robotics systems. The development of advanced technological capabilities for manufacturing of such reducers today gives the possibility for implementation of essential features of such devices: high efficiency, high gear ratio, kinematic accuracy and smooth motion. The presence of an adequate mathematical model gives the possibility for adjusting kinematic accuracy of the reducer by rational selection of manufacturing tolerances for its parts. This makes it possible to automate the design process for cycloid reducers with account of various factors including technological ones. A mathematical model and mathematical technique have been developed giving the possibility for modeling the kinematic error of the reducer with account of multiple factors, including manufacturing errors. The errors are considered in the way convenient for prediction of kinematic accuracy early at the manufacturing stage according to the results of reducer parts measurement on coordinate measuring machines. During the modeling, the wheel manufacturing errors are determined by the eccentricity and radius deviation of the pin tooth centers circle, and the deviation between the pin tooth axes positions and the centers circle. The satellite manufacturing errors are determined by the satellite eccentricity deviation and the satellite rim eccentricity. Due to the collinearity, the pin tooth and pin tooth hole diameter errors and the satellite tooth profile errors for a designated contact point are integrated into one deviation. Software implementation of the model makes it possible to estimate the pointed errors influence on satellite rotation angle error and reasonable selection of accuracy parameters for technological processes related to reducer parts manufacture. Additionally, it gives the possibility for estimation of the reducer kinematic error according to measurements by means of a coordinate measuring machine and diagnostics of reducer parts manufacturing errors by means of its kinematogram analysis. The model is implemented as a program developed in Microsoft Visual C++ 6.0 environment. Obtained results have found their application in CAD of cycloid reducers.
Keywords: modeling, planetary gearbox, pin-gear drive, cycloid gear, kinematic accuracy, manufacturing error
Acknowledgements. The paper has been prepared as a result of R&D work "Creating of high-tech production of precision high-performance forceful brand-new electromechanical actuators " in ITMO University, under financial support from the Russian Federation Ministry of Education and Science, according to the enactment of the Russian Federation Government dated April 9, 2010 № 218 "Measures of state support for development of cooperation between Russian universities, research organizations and companies which implement complex projects for high-tech production".
References
Acknowledgements. The paper has been prepared as a result of R&D work "Creating of high-tech production of precision high-performance forceful brand-new electromechanical actuators " in ITMO University, under financial support from the Russian Federation Ministry of Education and Science, according to the enactment of the Russian Federation Government dated April 9, 2010 № 218 "Measures of state support for development of cooperation between Russian universities, research organizations and companies which implement complex projects for high-tech production".
References
1. Litvin F.L. Teoriya Zubchatykh Zatseplenii [Theory of Gearing]. Moscow, Nauka Publ., 1968, 584p.
2. Litvin F.L. Gear Geometry and Applied Theory. 2nd ed. Cambridge University Press, 2004, 800 p.
3. Kudryavtsev V.N. Planetarnye Peredachi [Planetary Transmission]. Moscow, Leningrad, MashinostroeniePubl.,1966, 307 p.
4. Shannikov V.M. Teoriya i konstruirovanie reduktorov s vnetsentrennym tsikloidal'nym zatsepleniem [Theory and design of gears with eccentrically cycloidal engagement]. In Zubchatye i Chervyachnye Peredachi
[H-pole Serrated and Worm Gears]. Moscow, Leningrad, Mashgiz Publ.,1959, pp. 74–79.
[H-pole Serrated and Worm Gears]. Moscow, Leningrad, Mashgiz Publ.,1959, pp. 74–79.
5. Dascalescu A. Contribution to the Kinematics and Dynamics Studys of the Planetary Gears with Cycloid Toothing and Roller Teeth, PhD Theses. Cluj-Napoca, Romania, 2005. 9 p.
6. Fedosovskii M.E., Aleksanin S.A., Nikolaev V.V., Yegorov I.M., Dunaev V.I., Puctozerov R.V. The effect of
a cycloid reducer geometry on its loading capacity. World Applied Sciences Journal, 2013, vol. 24, no. 7, pp. 895–899. doi:10.5829/idosi.wasj.2013.24.07.13352
a cycloid reducer geometry on its loading capacity. World Applied Sciences Journal, 2013, vol. 24, no. 7, pp. 895–899. doi:10.5829/idosi.wasj.2013.24.07.13352
7. Bruevich N.G. Tochnost' Mekhanizmov [Accuracy of Mechanisms]. Moscow, Leningrad, GITTL Publ., 1946, 332 p.
8. Litvin F.L. Proektirovanie Mekhanizmov i Detalei Priborov [Design of Machinery and Parts of Devices]. Leningrad, Mashinostroenie, 1973, 695 p.
9. Sergeev V.I. Metodologicheskie osnovy povysheniya tochnosti mekhanizmov s vysshimi kinematicheskimi parami [Methodological basis of improving the accuracy of mechanisms with higher kinematic pairs]. Problemy Mashinostroeniya i Nadezhnosti Mashin, 2006, no.1, pp. 3–9.
10.Guan T.M. Calculation and analysis on the return error resulting from cycloid-disk modification in the cycloid drive. Modular Machine Tool and Automatic Manufacturing Technique, 2001, vol. 10, pp. 15–18.
11.Hidaka T., Wang H., Ishida T., Matsumota K., Hashimota M. Rotational transmission error of K-H-V planetary gears with cycloid gear. Transactions of the Japan Society of Mechanical Engineers Series C, 1994, vol. 60, no. 570, pp. 645–653.
12.Li C., Liu J., Sun T. Study on transmission precision of cycloidal pin gear in 2K-V planetary drives. Chinese Journal of Mechanical Engineering, 2001, vol. 37, no. 4, pp. 61–65.
13.Shirokoshi N., Hidaka T., Kasei S. Studies of influences of geometrical errors to final performances in small backlash planetary gears. Relations among position deviations of planet gears, target of backlash and non-working flank load. Transactions of the Japan Society of Mechanical Engineers Series C, 2000, vol. 66, no. 646, pp. 1950–1958.
14.Sun Y.G., Zhao X.F., Jiang F., Zhao L, Liu D, Lu G.B. Backlash analysis of RV reducer based on error factor fensitivity and Monte-Carlo simulation. International Journal of Hybrid Information Technology, 2014, vol. 7, no. 2, pp. 283–292.
15.Yang D.C.H., Blanche J.G. Design and application guidelines for cycloid drives with machining tolerances. Mechanism and Machine Theory, 1990, vol. 25, no. 5, pp. 487–501.